How to stop mikuni carb from running lean? This guide provides a comprehensive approach to diagnosing and resolving lean running issues in Mikuni carburetors. Understanding the symptoms, jetting, air leaks, fuel delivery, and maintenance is crucial for restoring optimal engine performance. Properly addressing these elements ensures a smooth and efficient running engine, crucial for any vehicle or machine relying on a Mikuni carb.
Identifying the specific cause of a lean condition is the first step. Symptoms like rough idling, hesitation, and poor acceleration are often indicators. Inspecting the carburetor visually and mechanically for air leaks or improper jetting is vital for pinpointing the problem.
Identifying the Lean Condition
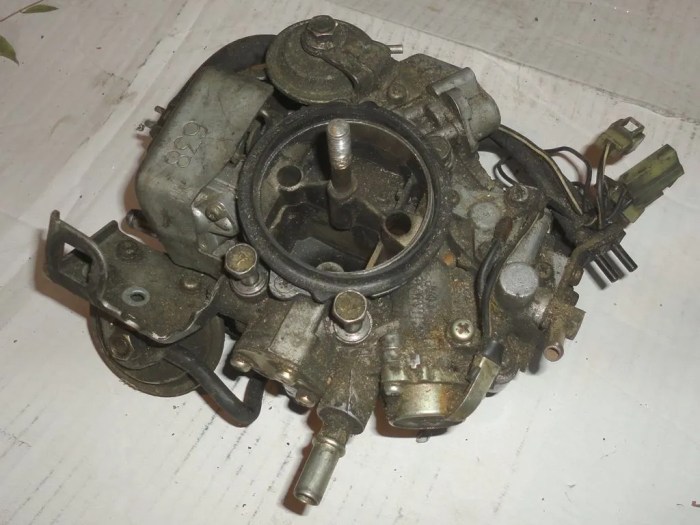
A Mikuni carburetor running lean presents a distinct set of symptoms, easily distinguishable from other common issues. Recognizing these signs is crucial for timely diagnosis and effective troubleshooting, preventing further damage to the engine. Proper identification allows for targeted adjustments to restore optimal performance.Lean running, a condition where insufficient fuel mixes with the air entering the engine, can manifest in various ways.
Distinguishing it from other carburetor problems like flooding or running rich requires careful observation of engine performance, exhaust characteristics, and visual inspection points.
Symptoms of Lean Running
Lean running is characterized by a noticeable drop in engine power and performance. The engine may sputter, hesitate, or even stall, especially under load. The lack of sufficient fuel can cause an erratic and uneven power delivery. A noticeably rough idle is a frequent symptom. The engine might feel weak and underpowered, particularly when accelerating.Exhaust emissions provide further clues.
Lean combustion often produces a noticeably “thin” or “stinging” exhaust smell. The exhaust color may also exhibit unusual characteristics, ranging from a pale blue to a nearly white or even colorless appearance, unlike the rich, dark, and dense exhaust seen in a correctly operating engine. This is due to incomplete combustion. Visual inspection of the exhaust system is important.
Visual Inspection Points
Visual inspection of the engine and carburetor components provides valuable insights into potential issues. Check for excessive heat buildup around the carburetor and intake manifold. Overheating in these areas often points to lean running and poor fuel mixture. Examine the spark plug for indications of lean running. A lean condition often manifests as a pale, light gray, or even white-colored spark plug.
The spark plug will also often exhibit a characteristically “darker” appearance than a rich spark plug.
Distinguishing Lean Running from Other Issues
Lean running differs from flooding, a condition where excessive fuel overwhelms the engine. Flooding manifests as a very wet engine, often with white smoke. Running rich, on the other hand, is characterized by an overly dense fuel-air mixture, leading to black exhaust smoke. A rich engine will also typically run smoothly, though possibly with excessive fuel consumption.
Mechanical Inspection
Thorough mechanical inspection of the carburetor is essential. Remove the air filter and visually inspect the air filter housing for any cracks, holes, or other signs of air leaks. Inspect the throttle body and any vacuum lines for cracks or other damage that could lead to air leaks. A leak in the fuel line or delivery system can cause lean running.
Verify that all connections are secure and that no fuel is leaking.
Potential Causes of Lean Running
Cause | Symptom | Potential Solution |
---|---|---|
Improper Jetting | Engine sputters, hesitates, or stalls; uneven power delivery; pale or colorless exhaust | Adjust pilot jet, main jet, and/or needle jet sizes |
Air Leaks | Engine sputters, hesitates, or stalls; uneven power delivery; pale or colorless exhaust; engine overheating | Identify and seal any leaks in intake system, vacuum lines, or gaskets |
Faulty Fuel Delivery System | Engine sputters, hesitates, or stalls; uneven power delivery; pale or colorless exhaust; possible fuel starvation | Check fuel pump, fuel lines, and fuel filter for proper function; ensure correct fuel level |
Understanding Jetting
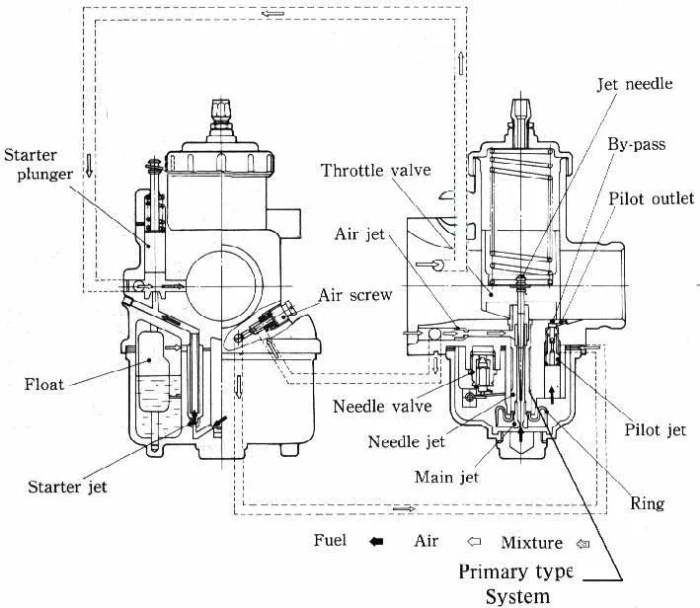
Mikuni carburetors, crucial components in many small engines, precisely control the fuel-air mixture for optimal performance. Understanding the intricate relationship between different jets is paramount to fine-tuning your engine’s fuel delivery. Correct jetting ensures efficient combustion, power output, and reduced emissions.The Mikuni carburetor’s complex jetting system plays a vital role in delivering the precise fuel-air mixture for optimal engine performance.
Different jets control fuel flow at varying engine speeds, enabling a smooth transition from idle to high RPMs. Accurately selecting jets is crucial for maintaining proper fuel delivery, preventing lean or rich conditions, and ensuring a responsive and powerful engine.
Function of Mikuni Carburetor Jets
The Mikuni carburetor utilizes a series of jets to precisely meter fuel flow at different engine speeds. Each jet plays a specific role in the fuel delivery system. The main jet, pilot jet, and needle jet, work in concert to regulate fuel delivery across the entire engine speed range.
Main Jet
The main jet is the largest jet in the system and primarily controls fuel delivery at higher engine speeds. Visualize it as a primary valve for fuel flow during acceleration and high-load operation. Its size directly affects the amount of fuel available to the engine at these speeds. Larger main jets allow more fuel flow, while smaller main jets restrict it.
Pilot Jet
The pilot jet is a smaller jet, located near the throttle valve, and regulates fuel flow at idle and low engine speeds. It’s crucial for starting and maintaining a stable idle. Its size determines the fuel delivery at low RPMs, impacting the engine’s ability to smoothly transition from idle to higher speeds.
Needle Jet
The needle jet, situated within the main jet area, adjusts fuel flow based on throttle position. Imagine it as a variable valve, controlling fuel flow in proportion to throttle opening. This allows for an appropriate fuel-air mixture as the engine’s load and speed increase.
Relationship Between Jets
The main jet, pilot jet, and needle jet work in tandem to ensure a consistent fuel mixture across the entire engine speed range. The pilot jet manages low RPMs, while the main jet handles higher RPMs. The needle jet adjusts fuel delivery dynamically as the throttle opens and closes, maintaining a consistent mixture throughout the operating range.
Jet Size Comparison
Different jet sizes directly impact the fuel mixture. Larger jet sizes allow more fuel to pass through, resulting in a richer mixture. Smaller jet sizes restrict fuel flow, leading to a leaner mixture. A precise balance between jet sizes is essential for optimal engine performance.
Selecting Correct Jet Sizes
Choosing the correct jet sizes is crucial for optimal engine performance in various conditions. Factors such as engine type, altitude, and load influence the required fuel mixture. Higher altitudes require leaner mixtures due to thinner air, while heavier loads necessitate richer mixtures. Consult your engine’s specifications or a reliable manual for guidance on selecting appropriate jet sizes.
Jetting Configurations and RPM Ranges
Jet Size | Engine RPM | Fuel Mixture |
---|---|---|
170 Main, 38 Pilot, 45 Needle | Idle to 3000 RPM | Lean |
175 Main, 40 Pilot, 45 Needle | Idle to 4000 RPM | Slightly Richer |
180 Main, 42 Pilot, 45 Needle | Idle to 5000 RPM | Rich |
This table provides a general guideline for different jetting configurations. The precise jetting requirements may vary based on specific engine models and conditions. Always consult your engine’s manual for specific recommendations.
Troubleshooting Air Leaks
Air leaks in a Mikuni carburetor can significantly impact its performance, leading to a lean running condition. Identifying and sealing these leaks is crucial for achieving optimal fuel-air mixture and engine power. This section will detail common locations for air leaks, provide a methodical procedure for detection, and suggest effective sealing techniques.
Common Air Leak Locations
Air leaks can occur in various areas of a Mikuni carburetor setup. Understanding potential leak points allows for a focused inspection process.
- Throttle Body Gaskets: These gaskets seal the throttle body to the carburetor body. Cracks, tears, or improper seating of the gasket can create significant air leaks. The gasket’s integrity is critical for a consistent air-fuel ratio.
- Throttle Shaft and Linkage: Any gaps or play in the throttle shaft or linkage system allows for unintended air intake. A loose connection or a worn-out linkage component can disrupt the proper throttle operation.
- Carburetor Body to Manifold Connections: The connection between the carburetor and intake manifold can leak if the mating surfaces are rough or improperly sealed. Proper manifold gasket seating is essential for maintaining a consistent air-fuel mixture.
- Fuel Inlet/Outlet Fittings: Loose or damaged connections on the fuel inlet or outlet lines can allow for air to enter the system. Inspect these areas meticulously for any signs of leakage.
- Vacuum Lines and Connections: Vacuum lines, if cracked or disconnected, can create leaks. Ensure all vacuum lines are securely connected and free of cracks or damage. These lines often lead to vacuum-dependent components like the power valve.
- Carburetor Base or Housing: Leaks can occur around the carburetor base or housing. Check for any cracks, gaps, or signs of deterioration in this area.
Identifying Air Leaks
Locating air leaks can be challenging but becomes more straightforward with a systematic approach.
- Visual Inspection: Carefully examine all visible connections and components for any signs of leaks. Look for signs of moisture or oil around gaskets, fittings, and connections. Visual examination should also include a check for cracks or breaks in the material.
- Leak Detection Spray: A leak detection spray can help pinpoint air leaks. Apply the spray to suspected areas and listen for a hissing sound or observe for bubbles forming around the leak site. This technique allows for accurate identification of leaks.
- Engine Operation: With the engine running, carefully inspect the connections and components. Listen for hissing sounds or a change in the engine’s operation. A lean running condition can be a clear indicator of air leaks.
- Manifold Pressure Test (Advanced): For a more thorough inspection, a manifold pressure test can be performed. This test involves measuring the pressure within the intake manifold to identify any pressure drop. A drop in pressure often indicates a leak.
Sealing Air Leaks
Sealing air leaks requires careful selection of materials and meticulous application.
- Gasket Replacement: Damaged gaskets should be replaced with new, high-quality gaskets. Ensure proper seating of the gaskets and use the appropriate sealant if necessary.
- Silicone Sealant: Silicone sealant is a versatile material for sealing air leaks, especially around difficult-to-reach areas. Apply a thin, even layer of silicone sealant to the affected areas.
- Thread Seal Tape: Thread seal tape is suitable for sealing threaded connections. Apply the tape in a spiral pattern to the threads before connecting the components.
- High-Temperature RTV Sealant: For high-temperature applications, high-temperature RTV sealant provides an effective solution. Apply a thin layer of sealant to the joint and allow it to cure according to the manufacturer’s instructions.
Troubleshooting Procedures
To address an air leak, a systematic approach is essential.
- Identify the Leak Location: Using the methods Artikeld above, pinpoint the exact location of the leak. This step is crucial for targeted repairs.
- Clean the Area: Thoroughly clean the area around the leak before applying any sealant. Removing dirt, debris, or old sealant will ensure proper adhesion.
- Apply Sealant: Apply the appropriate sealant to the leak site, ensuring a complete seal. Follow the manufacturer’s instructions for curing time.
- Reassemble: Carefully reassemble the components, ensuring proper alignment and tightness.
- Test: Start the engine and perform a thorough check for any remaining leaks. Listen for hissing sounds and observe the engine’s operation. If the problem persists, repeat the troubleshooting process.
Adjusting Fuel Delivery
Fine-tuning the fuel delivery system is crucial for achieving the optimal air-fuel mixture in a Mikuni carburetor. Incorrect float levels can lead to a lean condition, resulting in poor engine performance, rough idling, or even engine stall. This section details the procedures for adjusting the float level, fuel pump, and fuel lines, along with the impact of these adjustments on the overall engine performance.
Float Level Adjustment Procedure
Precisely adjusting the float level is vital for maintaining the correct fuel supply. The float acts as a crucial component, ensuring a consistent fuel level within the carburetor bowl. A properly adjusted float level maintains the correct fuel supply for the engine’s needs, preventing either flooding or starvation. Incorrect float level adjustment can significantly impact the engine’s performance, causing it to run lean or rich.
To adjust the float level, first, locate the float adjustment screw. This is typically a small, slotted screw on the underside of the float chamber. Use a small screwdriver to carefully adjust the screw, raising or lowering the float. Slight adjustments can significantly affect the fuel delivery. Over-tightening should be avoided.
The float should be adjusted so that the fuel level is just below the bottom of the fuel jet. This level is critical for ensuring the correct amount of fuel is delivered to the engine.
Impact of Float Height on Fuel Delivery and Mixture
The float height directly influences the amount of fuel drawn into the carburetor. A higher float level results in a higher fuel level in the bowl, leading to an over-rich mixture. Conversely, a lower float level leads to a lower fuel level, resulting in a lean mixture. The relationship is directly proportional. A slight variation in float height can noticeably impact the engine’s performance.
A lean mixture will cause the engine to run hot and potentially damage components. Conversely, a rich mixture may cause the engine to run poorly and produce excessive emissions.
Fuel Pump or Related Component Adjustment
Adjusting the fuel pump, if applicable, involves examining the pump’s pressure and flow rate. The fuel pump’s primary function is to supply fuel at the appropriate pressure to the carburetor. If the pump isn’t functioning correctly, the carburetor will not receive the necessary fuel, leading to a lean condition. Troubleshooting the fuel pump requires a thorough examination of its components and connections.
If the fuel pump is a mechanical pump, inspect the pump’s diaphragm, valves, and springs for any damage or wear. If the pump is electric, ensure the wiring is intact and the pump is receiving power.
Fuel Line and Related Component Inspection
Inspecting the fuel line and related components is essential for ensuring a consistent fuel supply. Clogged fuel lines, leaks, or kinks in the fuel line can impede fuel flow, leading to a lean condition. Carefully examine the fuel line for any signs of damage, such as cracks, splits, or kinks. Replace any damaged fuel lines immediately to avoid fuel leaks and ensure proper fuel delivery.
Also, check for any leaks in the fuel tank, fuel filter, or other related components.
Float Level Effects on Engine Performance
Float Level | Engine Response | Possible Issues |
---|---|---|
Too High | Engine runs rich, potentially floods | Poor acceleration, rough idling, excessive fuel consumption |
Too Low | Engine runs lean, potentially stalls | Poor acceleration, rough idling, engine overheating, potential damage to engine components |
Correct | Engine runs smoothly, consistent performance | No issues |
Maintenance and Prevention: How To Stop Mikuni Carb From Running Lean
Proper maintenance is crucial for a Mikuni carburetor to function optimally and avoid lean running conditions. Regular cleaning and inspection prevent gradual deterioration, ensuring consistent fuel delivery and preventing performance issues. This section details essential maintenance steps and preventative measures to maintain your Mikuni carburetor’s health.
Regular Maintenance Checklist
Regular maintenance is key to preventing lean running conditions. A thorough checklist ensures you address critical components.
- Visually inspect the carburetor body for any signs of damage, cracks, or corrosion. Look for any physical damage, like dents or scratches, that could impact airflow or fuel delivery.
- Inspect the fuel passages, jets, and float bowl for debris, dirt, and varnish buildup. Use a flashlight to meticulously check for any blockages or unusual deposits that could be affecting the fuel flow.
- Examine the throttle linkage and cable for smooth operation and proper adjustment. Ensure there are no kinks, binding points, or wear in the throttle assembly, as these can cause inconsistent throttle response.
- Check the air filter for cleanliness and proper function. A clogged air filter restricts airflow, forcing the carburetor to run lean. A clean filter is essential for optimal performance.
- Verify the float level is correct. An incorrect float level affects the amount of fuel delivered, potentially leading to either flooding or lean running. Use a precision gauge for accurate measurements.
Cleaning the Carburetor
Cleaning the carburetor is a crucial maintenance task. Proper cleaning ensures optimal fuel delivery and prevents lean running.
- Disassemble the carburetor: Carefully remove the carburetor from the engine, and use appropriate tools and techniques to disassemble it following the manufacturer’s instructions. Take pictures or make detailed notes of the original configuration for reassembly.
- Cleaning Agents: Use a non-corrosive carburetor cleaner (such as a spray cleaner). Avoid harsh chemicals that could damage the carburetor components. For stubborn deposits, a degreaser or a mixture of warm water and mild detergent might be needed.
- Cleaning Procedure: Thoroughly clean each component with a soft brush or compressed air, ensuring no residue remains. Submerge the removable parts in the cleaning agent, ensuring all surfaces are covered. Use a soft brush to clean all crevices and jets. Be very careful not to damage any small components during the process.
- Drying: Allow all parts to dry completely before reassembly. Use compressed air to remove any remaining moisture. Ensure the parts are thoroughly dry to prevent corrosion or malfunction.
- Reassembly: Reassemble the carburetor components in the reverse order of disassembly, carefully aligning all parts. Double-check all connections for proper seating.
Preventing Lean Running Conditions
Preventing lean running involves several proactive measures. Consistent maintenance is key to avoiding this issue.
- Proper Air Filter Maintenance: Regularly replace or clean the air filter to ensure consistent airflow. A clogged filter can force the engine to run lean.
- Fuel Quality: Use high-quality gasoline with the recommended octane rating for your engine. Poor fuel quality can contribute to lean running conditions.
- Proper Fuel Delivery System: Check and adjust the fuel delivery system components to ensure the proper fuel mixture is maintained. Ensure the fuel lines are free from blockages or leaks.
- Regular Tune-ups: Keep your engine tuned up. A well-maintained engine contributes to a consistent fuel mixture and prevents lean running.
Storage Procedures
Proper storage procedures for the carburetor prevent damage and ensure its readiness for use.
- Cleaning: Thoroughly clean the carburetor before storage, ensuring all traces of fuel and contaminants are removed.
- Drying: Allow the carburetor to dry completely. This prevents corrosion and damage during storage.
- Protection: Store the carburetor in a clean, dry, and cool environment. Protecting it from extreme temperatures or moisture is essential.
- Sealing: Seal the carburetor in a protective container to prevent dust and debris from entering the carburetor.
Advanced Troubleshooting
Beyond basic jetting and air leaks, more intricate issues can cause a Mikuni carburetor to run lean. These problems often involve the interplay of multiple components and require a systematic approach to diagnosis. Understanding these advanced troubleshooting steps is crucial for achieving optimal performance and preventing potential engine damage.
Vacuum Leaks
Vacuum leaks, often subtle and difficult to pinpoint, can significantly impact fuel delivery, resulting in a lean running condition. These leaks can manifest as a hissing sound or a pressure drop within the intake system. Pinpointing their location is key to effective repair.
- Visual Inspection: A thorough visual inspection of all hoses, clamps, and gaskets connected to the intake manifold and carburetor is essential. Look for cracked, deteriorated, or loose connections. Inspect the gaskets between the carburetor and manifold for damage or misalignment. A telltale sign might be a visible crack or a noticeable bulge in a rubber hose.
- Pressure Testing: A pressure testing method involves applying controlled pressure to the intake manifold and monitoring the pressure drop. This method can pinpoint the exact location of a leak. A pressure gauge, connected to the intake manifold, will show a gradual pressure drop if a leak is present. The pressure drop rate can be used to estimate the severity of the leak.
A leak in a manifold gasket, for instance, would exhibit a rapid pressure drop compared to a leak in a smaller hose.
- Smoke Testing: Smoke testing utilizes a smoke-generating solution introduced into the intake system. Any leaks will be visible as a plume of smoke escaping from the problematic area. This method is effective for detecting hard-to-spot leaks, such as those concealed behind engine components. This method can be used for both external and internal leaks within the intake system, which might otherwise be hard to identify.
Faulty Ignition System
A faulty ignition system can also lead to a lean condition. Ignition timing, spark plug condition, and coil function directly affect the combustion process. A mistimed spark or a weak spark can hinder proper fuel combustion, leading to a lean air-fuel mixture.
- Ignition Timing: Incorrect ignition timing can significantly affect the efficiency of fuel combustion. If the spark occurs too early or too late, the fuel may not burn completely, resulting in a lean condition. Proper timing is crucial for complete combustion and efficient fuel utilization. Incorrect timing can lead to an uneven power delivery or complete engine stall, and should be carefully checked against manufacturer specifications.
- Spark Plug Condition: A fouled or worn spark plug can hinder the proper ignition of the air-fuel mixture. Spark plugs should be inspected for fouling, excessive wear, or misalignment, and replaced if necessary. Carbon buildup on the spark plug can reduce its efficiency, leading to inconsistent spark strength and a lean condition. The color of the spark plug can be used to diagnose combustion issues, which can then be correlated to a lean condition.
- Coil Function: A malfunctioning coil can also lead to weak or inconsistent spark. The coil is responsible for producing the high voltage required to create a spark across the spark plug gap. A faulty coil will deliver a weak or inconsistent spark, leading to a lean condition. Testing the coil’s output voltage can help pinpoint the problem.
Diagnostic Tools
Several advanced diagnostic tools can assist in troubleshooting lean running conditions.
- Vacuum Gauge: A vacuum gauge is an important tool for detecting vacuum leaks. It measures the vacuum pressure within the intake manifold. A significant drop in vacuum pressure indicates a leak, helping to locate the problem area. Fluctuations in vacuum pressure, especially at varying engine speeds, can indicate a leak that is harder to identify using visual methods alone.
- Oscilloscope: An oscilloscope can analyze electrical signals from the ignition system. This can help diagnose issues like misfiring, weak sparks, and timing problems. An oscilloscope can display the waveforms generated by the ignition system, helping identify discrepancies from the expected signals, which can then be correlated to a lean condition.
Troubleshooting Flowchart
A systematic approach to troubleshooting is essential for diagnosing and resolving lean running issues. The following flowchart provides a structured approach.
Step | Action | Outcome |
---|---|---|
1 | Visual Inspection (hoses, clamps, gaskets) | Leaks identified? |
2 | Pressure Testing (if visual inspection fails) | Leaks identified? |
3 | Smoke Testing (if pressure testing fails) | Leaks identified? |
4 | Ignition Timing Check | Correct timing? |
5 | Spark Plug Inspection | Fouled or worn? |
6 | Coil Function Test | Faulty coil? |
7 | Adjust Carburetor Settings (if no leaks or ignition issues) | Lean condition resolved? |
Engine Performance and Tuning
Optimizing engine performance with a Mikuni carburetor requires understanding the intricate relationship between engine load and fuel requirements. Varying throttle positions, load conditions, and RPMs all impact the carburetor’s ability to deliver the precise fuel-air mixture for optimal combustion. This section details how to analyze and adjust engine settings to achieve peak performance under different operating conditions.Engine load significantly influences the fuel demand.
Heavier loads, such as accelerating uphill or pulling a load, require more fuel for adequate power output. Conversely, lighter loads, such as cruising at a constant speed, necessitate a leaner mixture to avoid excessive fuel consumption and potential engine damage.
Correlation Between Engine Load and Fuel Requirements
Engine load is directly proportional to the fuel demand. A heavier load necessitates a richer fuel mixture to provide sufficient power. A lighter load, on the other hand, requires a leaner mixture for efficiency. This relationship is crucial for proper carburetion and engine performance.
Adjusting Engine Settings for Varying Load Conditions
Fine-tuning the fuel delivery for different load conditions is essential for optimal engine performance. This involves adjusting the carburetor’s settings to match the changing fuel requirements. This is best done with a systematic approach.
- Idle Settings: At idle, the engine’s load is minimal. A precise idle mixture ensures smooth operation without stalling or excessive fuel consumption. Adjusting the idle mixture screw allows for this fine-tuning. Proper idle speed and mixture are essential for consistent engine operation.
- Mid-Range Performance: Mid-range performance demands a slightly richer mixture than idle but leaner than full throttle. Adjusting the main jet and pilot jet combination is crucial in this area. These adjustments allow for consistent acceleration and power delivery across the mid-range RPMs.
- Full Throttle: At full throttle, the engine operates at maximum load. This demands the richest fuel mixture possible. Careful selection of the main jet size is critical in this situation. The mixture should be rich enough to sustain the engine’s power needs but not so rich as to create a risk of flooding or damage.
Fine-tuning the Fuel Mixture for Peak Performance
Precise tuning of the fuel mixture is critical for achieving peak performance across all operating conditions. This involves a systematic approach and careful monitoring.
- Initial Settings: Start with the factory recommended settings as a baseline. This provides a starting point for adjustments.
- Load Testing: Test the engine under varying loads, from idle to full throttle, and note any performance issues, such as hesitation or sputtering. These tests provide valuable data for identifying areas needing adjustment.
- Mixture Adjustments: Gradually adjust the carburetor settings (idle mixture screw, pilot jet, main jet) based on the load testing results. This process is iterative and requires patience. Observe the engine’s response to each adjustment to determine the optimal setting.
Examples of Engine Tuning Techniques, How to stop mikuni carb from running lean
Different engine tuning techniques, such as the “methodical approach” and the “progressive adjustment” technique, offer varying strategies for fine-tuning the fuel mixture.
- Methodical Approach: This involves systematically adjusting each carburetor component (pilot jet, main jet, idle mixture screw) while monitoring engine performance at different load conditions. Each adjustment should be made in small increments and validated by testing the engine’s response. This allows for precise tuning.
- Progressive Adjustment: This involves gradually adjusting the main jet size and pilot jet size while monitoring the engine’s performance under varying load conditions. This method focuses on optimizing fuel delivery across the entire RPM range. Adjustments are made in small increments and the engine is monitored closely.
Conclusive Thoughts
Troubleshooting a lean-running Mikuni carburetor involves a systematic approach. By understanding jetting, identifying and sealing air leaks, adjusting fuel delivery, and performing regular maintenance, you can optimize your engine’s performance. This guide provides a practical framework for resolving lean running issues. Remember, proper maintenance is key to preventing future problems.
FAQ Guide
What are the common symptoms of a Mikuni carburetor running lean?
Common symptoms include rough idling, hesitation, poor acceleration, and a noticeably rich or lean smell in the exhaust. The engine may also show signs of overheating.
How often should I clean and inspect my Mikuni carburetor?
Regular cleaning and inspection, typically every 50-100 hours of operation, depending on the environment and usage, are essential for optimal performance and to prevent lean running issues.
What are some advanced troubleshooting techniques for lean running?
Advanced troubleshooting may involve checking for vacuum leaks, using diagnostic tools to measure fuel pressure, and examining the ignition system for issues.
What tools are helpful for identifying air leaks in a Mikuni carburetor?
A leak down tester, smoke machine, or even a spray bottle of soapy water can be helpful tools for finding air leaks.