How to shim a starter sets the stage for a detailed guide on this crucial automotive repair. Understanding the process is vital for anyone working on vehicles, and this comprehensive guide will walk you through every step, from initial assessment to troubleshooting common problems.
Shimming a starter motor involves adjusting its position or alignment to ensure proper engagement with the engine. This often becomes necessary due to wear and tear, misalignment, or other factors. Proper shimming is crucial for optimal starter performance, preventing damage, and extending the lifespan of your vehicle’s electrical system.
Introduction to Shimming a Starter
Ever feel like your car’s starter is struggling to crank the engine? Sometimes, a simple solution lies in a seemingly small component: shimming. Shimming a starter motor involves adding thin, flat pieces of material (shims) between the starter and the engine block or other mounting points. This seemingly minor adjustment can significantly impact the starter’s performance.The purpose of shimming is to correct alignment issues or compensate for wear and tear.
A misaligned starter can lead to poor engagement with the flywheel, resulting in a weak or intermittent cranking effort. By adding shims, you effectively adjust the spacing, ensuring proper engagement and a smoother start-up process. This is crucial for optimal engine performance and longevity. Often, this small adjustment is all it takes to get a stubborn engine firing up again.
Typical Scenarios Requiring Starter Shimming
Starter motors, like any mechanical component, can wear down over time. This wear can cause misalignment, which necessitates shimming. This often happens due to several factors, including engine vibrations, impact damage, or improper installation. The resulting misalignment can lead to issues ranging from weak cranking to complete failure. Understanding these scenarios helps in diagnosing starter problems effectively.
Types of Starters and Common Shimming Reasons
Starter Type | Common Reasons for Shimming |
---|---|
Automotive Starters (various models) | Wear and tear of the starter mounting surfaces, engine vibration, improper installation, and damage caused by accidents. |
Industrial Starters (for heavy machinery) | Misalignment due to heavy-duty usage, impacts from operating conditions, and thermal expansion/contraction from high operating temperatures. |
Marine Starters (boat engines) | Vibration and shock from the boat’s movement, possible corrosion and wear from exposure to moisture and salt, and the need to compensate for varying mounting positions. |
Tools and Materials Required
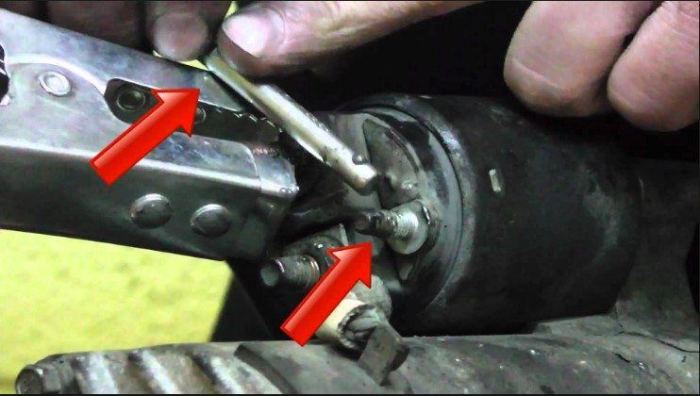
Getting your starter motor shimmed right requires the right tools and materials. A well-equipped toolbox is key to a smooth and successful repair. Improper tools can lead to damage and wasted time. This section details everything you need to know about the essential tools and materials for the job.Shimming a starter motor, like any mechanical repair, demands precision.
The right tools are crucial for achieving a precise fit, ensuring optimal performance, and preventing potential issues. Using the correct shims also prevents damage to the starter motor and other components in the engine.
Essential Tools
A comprehensive toolkit is your best friend in this process. Having the right tools will save you time and frustration. These tools are necessary for accurate measurements, secure mounting, and precise adjustments.
- Torque wrench: Critical for ensuring proper tightening of bolts and screws, preventing over-tightening that could damage components. A torque wrench ensures consistent and safe tightening.
- Socket set: Various sizes are needed for different bolts and nuts throughout the process. This set should include sockets for various head shapes and sizes.
- Screwdrivers: Phillips and flathead screwdrivers are essential for removing and securing various parts. Ensure you have the right size for each screw.
- Measuring tools: A ruler, caliper, or micrometer for accurate measurements of the starter’s components and the shims. Precise measurements ensure proper fit.
- Hammer: Necessary for gently tapping components into place, ensuring they are aligned correctly. A soft-faced hammer is recommended to avoid damaging components.
- Wire brush: For cleaning the surfaces of the starter motor and mounting points, ensuring a clean and secure fit. A wire brush removes rust and debris.
Types of Shims
Shims come in various materials and thicknesses, each tailored to specific needs. Choosing the correct shim is vital for optimal performance.
- Steel Shims: Commonly used due to their durability and ability to withstand significant pressure. They are robust and maintain their shape under load. For example, in heavy-duty applications like trucks, steel shims are a practical choice.
- Aluminum Shims: Lighter than steel shims, they are suitable for applications where weight is a concern. They are often chosen for their flexibility and ability to absorb vibrations. In a car, aluminum shims can help with engine noise reduction.
- Brass Shims: Known for their corrosion resistance, they are often used in environments prone to moisture or humidity. They resist rust and are suited for harsh conditions. This is a common choice for marine engines.
Shim Specifications and Applications
The table below provides a comprehensive guide to different shim types and their appropriate applications. Matching the right shim to the task is crucial.
Shim Type | Material | Thickness Range | Application |
---|---|---|---|
Steel | Steel | 0.010″ to 0.125″ | Heavy-duty applications, high-torque environments |
Aluminum | Aluminum | 0.005″ to 0.075″ | Applications needing lighter weight, vibration absorption |
Brass | Brass | 0.002″ to 0.050″ | Applications requiring corrosion resistance, like marine environments |
Materials
In some cases, specific materials are needed for the process. These materials ensure a clean and secure repair.
- Cleaning solvent: For cleaning surfaces and removing debris, ensuring a clean and secure mounting area. A solvent will remove grime and contaminants.
Safety Precautions
Shimming a starter, while a relatively straightforward task, involves handling potentially hazardous components. Ignoring safety precautions can lead to injuries ranging from minor burns to serious electrical shocks. Therefore, prioritizing safety is paramount throughout the entire process. Understanding the potential hazards and taking the necessary precautions will ensure a safe and successful outcome.
Electrical Hazards
Electrical components are integral to starter operation. Improper handling can result in electric shocks. Ensure the power is completely disconnected from the circuit before commencing any work. A properly functioning multimeter is crucial for verifying the circuit’s power status. Failure to disconnect the power supply can lead to dangerous electrical shocks.
Always double-check the power switch to guarantee the circuit is completely off.
Potential for Burns
The starter components can become extremely hot during operation, potentially causing burns. Allow ample time for the components to cool down before handling them. Always use heat-resistant gloves and protective eyewear to prevent accidental contact with the heated parts. Burns can occur from contact with heated metals and terminals.
Handling Materials
Some shimming materials, particularly metal components, can be sharp or have rough edges. Use caution when handling these materials to avoid cuts or abrasions. Always wear appropriate gloves to prevent cuts and minimize the risk of injury. If using any cutting tools, ensure they are sharp and properly maintained to prevent accidental slips and injuries.
Important Safety Measures
Following these crucial safety measures will significantly reduce the risk of accidents during the shimming process:
- Disconnect Power Supply: Always disconnect the power supply to the starter motor before starting any work. Failure to do so can result in severe electric shock.
- Use Insulated Tools: Employ insulated tools and gloves to avoid electric shock. Ensure the tools are in good condition and free from damage.
- Wear Protective Gear: Wear safety glasses, gloves, and closed-toe shoes to protect yourself from flying debris, sharp edges, and potential burns. A safety vest is recommended for better visibility in a workshop environment.
- Proper Ventilation: If working in an enclosed space, ensure adequate ventilation to prevent the buildup of fumes or gases. This is especially important when using certain shimming materials.
- Work in a Well-Lit Area: Maintain a well-lit work area to minimize the risk of slips, trips, and falls. Poor visibility can lead to accidents.
- Keep the Work Area Clean: Maintain a clean and organized work area to prevent tripping hazards. Remove any unnecessary materials or tools to create a safe workspace.
- Seek Assistance When Needed: Don’t hesitate to seek assistance from a qualified professional if you encounter any difficulties or feel uncomfortable performing the shimming task yourself. Consult with a knowledgeable individual for help if needed.
Step-by-Step Procedure
Shimming a starter is a crucial maintenance step that can significantly impact its performance and longevity. Proper shimming ensures consistent baking results and prevents potential issues like uneven heating or premature wear. Following a precise procedure is key to achieving optimal results.This section details the step-by-step process for shimming a starter, emphasizing critical points and the correct sequence of actions.
Understanding these steps will allow you to confidently shim your starter, ensuring its optimal functionality.
Procedure for Shimming a Starter
Careful preparation and precise execution are vital for successful starter shimming. Incorrect shimming can lead to problems with the starter’s performance and lifespan. Following the steps Artikeld below ensures proper shimming and prevents potential issues.
- Preparation and Assessment: Carefully inspect the starter for any visible damage or irregularities. Note the current height and position of the starter. This assessment helps in determining the correct shim thickness and placement. This step is crucial for proper shimming.
- Selecting the Shim Material: Choose the appropriate shim material, ensuring it is non-reactive with the starter’s components. Common materials include thin metal sheets, wooden shims, or even appropriately sized and shaped pieces of cardboard or plastic. The choice of material is critical, as it will directly impact the functionality of the starter.
- Measuring and Cutting the Shim: Accurately measure the required shim thickness. This is determined by the desired height adjustment and the existing height of the starter. Cut the shim material to the precise dimensions. Precise measurement and cutting are essential for a consistent height adjustment. Ensure that the cut edges are smooth to prevent any issues with the starter’s operation.
- Placement of the Shim: Carefully place the shim under the starter base or in the designated shim area, ensuring it’s centered. Proper placement is essential for maintaining the starter’s balance and preventing any tipping or shifting during operation. The shim should be placed securely to prevent any movement during use.
- Testing and Adjustment: After placing the shim, test the starter’s operation. Observe if the height adjustment is satisfactory. If not, remove the shim and adjust the thickness or placement as needed. Repeat this process until the desired height and stability are achieved. This iterative testing process is important to ensure the starter operates at optimal height and stability.
Troubleshooting and Common Issues
Shimming a starter might seem straightforward, but unexpected hiccups can arise. Understanding potential problems and their solutions is crucial for a smooth and successful installation. Knowing how to diagnose and fix issues will save you time and frustration, ensuring your starter is properly aligned and functioning optimally.Troubleshooting involves identifying the root cause of any problem. This can range from simple miscalculations to more complex mechanical issues.
By systematically addressing potential problems, you can avoid costly repairs or replacements.
Potential Issues During Shimming, How to shim a starter
Proper shimming requires precision and attention to detail. Misalignment can lead to uneven wear and tear on the starter components, and potentially even damage.
- Incorrect Shim Thickness: Using the wrong shim thickness can result in either insufficient or excessive clearance between the starter and the engine block. This can lead to a grinding noise, or the starter may not engage the flywheel properly. Ensure accurate measurement of the necessary shim thickness and the correct placement of shims to maintain the required clearance.
- Damaged Shim Material: Bent, cracked, or deformed shims can affect the starter’s alignment and engagement. Using damaged shims can cause uneven wear and tear on the starter’s components. Always inspect shims for any signs of damage before installation. Replacing damaged shims with new ones is crucial for optimal performance.
- Insufficient Shim Material: Insufficient shim material may not provide the required clearance between the starter and the engine block. This can lead to the starter engaging with the flywheel at an angle, or the starter housing touching the engine block. Using enough shim material to create the appropriate clearance is critical for proper starter function. Ensure sufficient shim material is available to maintain the required clearance.
- Improper Shim Placement: Incorrect placement of shims can affect the starter’s alignment. Make sure to install shims according to the manufacturer’s specifications. This may include specific locations, or the number of shims needed. The starter’s alignment is crucial to prevent unnecessary wear and tear on components.
Diagnosing and Fixing Shim-Related Problems
A systematic approach is key to diagnosing and fixing shim-related issues.
- Visual Inspection: Carefully inspect the shims for any signs of damage or misalignment before installation. Look for bends, cracks, or deformations that could compromise the starter’s alignment.
- Measuring Clearance: Use a precise measuring tool to verify the clearance between the starter and the engine block. This measurement should align with the recommended specifications for the particular engine and starter. Using the right tools and methods will ensure accurate results.
- Checking for Grinding or Clicking Sounds: Pay close attention to any unusual noises, such as grinding or clicking, that might indicate issues with the starter engagement or alignment. These sounds often indicate a problem with the shims or the alignment of the starter components. Identify the sound and its origin for accurate diagnosis.
- Re-checking Measurements: If the starter doesn’t engage smoothly, re-measure the shim thickness and alignment. Verify the measurement process and correct any errors. Ensure the accuracy of your measurements for the required clearance.
Causes of Shim Failure and Corrective Measures
Shim failure can stem from several factors, requiring specific corrective measures.
- Excessive Vibration: Excessive engine vibration can cause the shims to loosen or shift over time. This can lead to the starter not engaging the flywheel properly. Addressing the vibration source is crucial to prevent future shim failure. This could include examining the engine mounts or other components causing vibrations.
- Material Degradation: Over time, the material used for shims might degrade, compromising their structural integrity. Using materials suitable for the specific application and environment is essential to prevent material degradation. Choosing high-quality, durable shims can prevent this problem.
- Corrosion: Corrosion on the engine block or starter components can affect the shim’s ability to maintain the proper clearance. Prevent corrosion by using protective measures and regularly maintaining the engine. Cleaning the affected areas thoroughly and applying anti-corrosion coatings can help.
Alternatives to Shimming: How To Shim A Starter
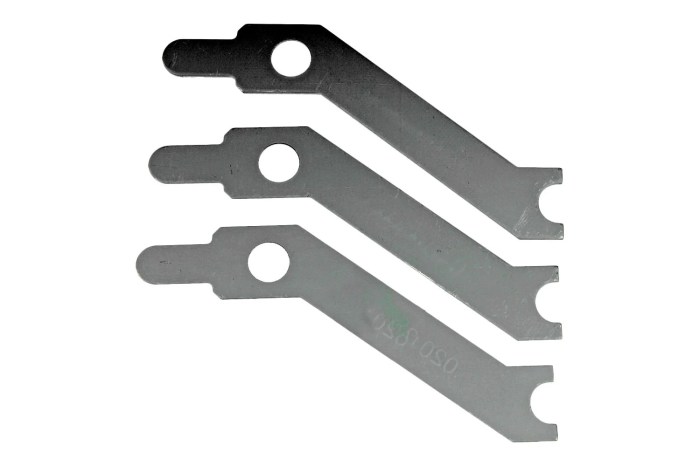
Sometimes, shimming a starter isn’t the only—or even the best—solution to a problematic starter. There are other methods to diagnose and fix the issue, each with its own set of advantages and disadvantages. Understanding these alternatives can help you choose the most effective approach for your specific situation.Beyond simply adjusting the starter’s position, other mechanical and electrical issues might be causing the problem.
This section will explore some of those alternatives, allowing you to tackle the root cause rather than just a symptom.
Starter Relay Issues
Starter relays are crucial components in the starter system. A faulty relay can prevent the starter from engaging, leading to a non-functional starter. Inspecting the relay for damage, corrosion, or loose connections is essential. Replacing a faulty relay is a relatively straightforward process, often resolving the issue without the need for more extensive work.
Starter Motor Issues
A damaged starter motor is another potential culprit. Signs of a bad starter motor include grinding noises, slow engagement, or complete failure to turn over the engine. If the motor itself is damaged, shimming won’t solve the problem. A damaged motor often requires replacement. The cost of a new starter motor can vary, but it’s often less expensive than a complete engine rebuild.
Wiring Issues
Electrical issues, like loose connections, corroded wires, or a faulty starter solenoid, can also lead to starter problems. Thorough examination of the wiring harness, checking for damage or poor connections, is crucial. Fixing these issues is often less involved than replacing the starter motor, and often involves careful cleaning, tightening, or replacing damaged wires.
Battery Problems
A weak or failing battery can cause a starter to struggle or fail to engage. Check the battery’s voltage and condition, and consider replacing it if necessary. A low battery can manifest as a slow crank, or no crank at all, and is a simple, yet effective, point of diagnosis.
Other Potential Solutions
- Checking the starter engagement mechanism: Ensure the starter engages properly. A sticking or jammed engagement mechanism can cause problems. Cleaning the mechanism and lubricating it may resolve the issue.
- Inspecting the engine’s electrical system: Look for issues with the electrical connections in the engine’s control system. A problem in the engine’s wiring can affect the starter’s operation. Careful inspection and repair of these electrical components could resolve the issue.
- Considering the possibility of a faulty ignition switch: A faulty ignition switch can prevent the starter from receiving the necessary power to engage. Inspecting the ignition switch for problems can be a key part of troubleshooting.
By systematically checking these alternatives, you can effectively identify the underlying cause of your starter issues and choose the most appropriate solution, saving time and potentially significant costs.
Specific Starter Models
Shimming a starter isn’t a one-size-fits-all process. Different starter models have varying internal components and assembly. Understanding the specific model you’re working with is crucial for a successful shim installation, avoiding potential damage and ensuring optimal performance. Knowing the starter’s make and model will help you determine the correct shim thickness and placement.
This section delves into specific starter models, offering detailed guidance on shimming procedures. Each section includes identification tips, specific instructions, and potential issues to watch out for. By following these detailed guides, you’ll be equipped to shim your starter correctly, extending its lifespan and maintaining optimal engine performance.
Bosch Starter Models
Bosch starters are widely used in various automotive applications. Proper identification is key to ensuring accurate shim installation. Look for the model number stamped on the starter housing. If unsure, consult the vehicle’s owner’s manual for specific details.
Starter Model | Identification | Specific Instructions | Potential Issues |
---|---|---|---|
Bosch 0 280 201 301 | Look for a stamped model number on the housing, often near the mounting bolts. | For this model, a 0.020″ shim is typically recommended for optimal engagement. Carefully measure the existing gap before installation to ensure proper alignment. Use a precise shim kit to maintain accuracy. | Improper shim selection can lead to premature starter wear. Over-shimming can cause excessive friction, leading to overheating. Under-shimming can result in inconsistent engagement and reduced power. |
Bosch 0 280 201 302 | Identify this model by its unique housing design and the model number stamped on it. | This starter often benefits from a 0.015″ shim. Always verify the correct shim thickness by consulting the manufacturer’s specifications. | Incorrect shim thickness can cause engagement problems, resulting in a grinding noise or complete failure to engage. |
AC Delco Starter Models
AC Delco starters are another popular choice. Similar to Bosch starters, model identification is essential. Usually, the model number is located on a plate on the starter housing.
Starter Model | Identification | Specific Instructions | Potential Issues |
---|---|---|---|
AC Delco 12345 | Look for the stamped model number near the mounting bracket or the label on the starter. | This model generally requires a 0.010″ shim. Ensure proper alignment and use a torque wrench to tighten mounting bolts to the manufacturer’s specifications. | Insufficient shim thickness might cause the starter to grind. Excessive shim thickness can lead to difficulty starting and excessive wear. |
AC Delco 67890 | Identify by the unique housing design and the model number on the starter. | For this model, a 0.025″ shim is commonly used. Confirm this with the manufacturer’s specifications. | Improper shim selection may lead to difficulties engaging the starter or excessive noise. |
Last Point
In conclusion, mastering the art of shimming a starter requires careful attention to detail, adherence to safety precautions, and a step-by-step approach. While shimming offers a reliable solution, understanding alternatives and specific starter model requirements is also important. This guide provides a comprehensive resource for tackling this task, enabling you to confidently maintain your vehicle’s essential components.
Answers to Common Questions
What are the typical causes of starter motor misalignment that necessitate shimming?
Wear and tear on the starter components, improper installation, or damage during previous repairs can lead to misalignment. This often results in the starter not engaging properly with the flywheel, causing difficulty or failure to start the engine.
What types of shims are commonly used for starter motors, and what materials are they made of?
Shims for starters are typically made of materials like steel, brass, or plastic, and come in various thicknesses. The specific material and thickness depend on the starter model and the required adjustment. Consult your repair manual or a mechanic for recommendations on appropriate shim types.
What safety precautions should I take when working on a starter motor?
Always disconnect the battery before performing any work on the starter motor. Wear appropriate safety glasses and gloves to protect yourself from flying debris or sharp edges. Work in a well-ventilated area to avoid inhaling fumes or dust.
What are some common troubleshooting steps if the starter motor still doesn’t engage properly after shimming?
Check the battery terminals for corrosion. Verify the starter solenoid is functioning correctly. Ensure the flywheel or other related components aren’t damaged or misaligned. Consult a mechanic if the issue persists.