How to integrate palletizers unlocks the potential for streamlined material handling and increased efficiency. This comprehensive guide dives deep into the intricate process, equipping you with the knowledge and strategies to seamlessly integrate palletizers into your operations. From understanding different palletizer types and their applications to navigating the complexities of software integration, we’ll explore every critical step. We’ll also examine industry best practices and future trends to prepare you for success in today’s dynamic manufacturing environment.
This detailed guide will provide a step-by-step approach to successfully integrating various types of palletizers, from vertical and horizontal to robotic systems. Understanding the nuances of each integration method, combined with crucial safety considerations, will be key to optimizing your workflow and maximizing ROI.
Introduction to Palletizing: How To Integrate Palletizers
Palletizing is a critical component of modern material handling, enabling efficient and safe movement of goods. It’s the process of stacking items onto a pallet, transforming loose products into a stable and easily transportable unit. This pivotal step streamlines warehousing, shipping, and receiving, ultimately enhancing overall operational efficiency.Palletizers are automated systems designed to perform this task. They represent a significant advancement in logistics, freeing up human labor from repetitive and potentially hazardous tasks, and drastically improving productivity.
Types of Palletizers
Palletizers come in various configurations, each tailored to specific needs. Understanding these differences is crucial for choosing the right system.
- Vertical Palletizers: These systems utilize a vertical stacking mechanism to quickly build pallets. They are often preferred for high-volume applications, especially when space is a constraint. The vertical design allows for compact layouts and high throughput. Consider a high-speed grocery store where fresh produce needs to be efficiently palletized; a vertical system would be an excellent choice.
- Horizontal Palletizers: Horizontal systems arrange items in a horizontal fashion, commonly used when items have specific placement requirements. They are frequently seen in environments where items are already organized in rows or have particular orientations. Imagine a factory assembling pre-cut parts; a horizontal palletizer would precisely position those parts on the pallet.
- Robotic Palletizers: These systems utilize robotic arms for precise placement of items on pallets. This approach offers greater flexibility and adaptability, allowing for a wider range of products. Robotic palletizers excel in situations where items have variable shapes or sizes. They are well-suited for diverse product lines, like a manufacturer handling a variety of electronic components.
Industries Utilizing Palletizers
Palletizing systems are not confined to a single industry. Their versatility allows for widespread application.
- Food and Beverage: Palletizers are essential for efficiently packaging and shipping various food items, from canned goods to frozen products. Imagine the vast volume of produce and dairy products needing to be quickly palletized for distribution.
- Retail: Palletizers play a critical role in the efficient handling of retail inventory. Imagine the daily influx of products arriving at a large retail distribution center; palletizers help quickly and safely store the incoming goods.
- Manufacturing: Palletizers are vital in numerous manufacturing processes. They facilitate the efficient packaging of manufactured goods, whether it’s electronics, machinery, or other products.
- Pharmaceuticals: The handling of pharmaceuticals requires precision and sterility. Palletizers are instrumental in the careful packaging and shipping of medication. Imagine the meticulous process of palletizing sensitive pharmaceuticals for distribution.
Benefits of Using Palletizers
Implementing palletizers offers numerous advantages, contributing significantly to operational efficiency.
- Increased Productivity: Palletizers automate the palletizing process, significantly reducing manual labor and increasing the speed at which products are handled. This translates to a substantial boost in overall throughput.
- Improved Safety: Automating the process of palletizing eliminates repetitive, potentially hazardous lifting and handling tasks, thereby minimizing the risk of workplace injuries.
- Enhanced Accuracy: Automated systems minimize human error, ensuring consistent and accurate palletizing, leading to fewer mistakes and wasted materials.
- Reduced Costs: While initial investment may be substantial, the long-term cost savings through increased efficiency, reduced labor costs, and minimized waste are substantial.
Choosing a Palletizer
Selecting the appropriate palletizer requires careful consideration of various factors.
- Product Characteristics: The size, shape, and weight of the products significantly influence the type of palletizer needed. A palletizer designed for bulky items would differ drastically from one used for smaller, more delicate products.
- Throughput Requirements: The volume of products that need to be palletized per hour is a critical factor in determining the required palletizer capacity.
- Budget Constraints: Palletizers range in price based on their features and capabilities. Understanding the budget available is essential for selecting a suitable system.
- Space Constraints: The available space in the warehouse or factory plays a crucial role in determining the size and type of palletizer that can be accommodated.
System Integration Considerations
Successfully integrating a palletizer into an existing production line is crucial for maximizing efficiency and minimizing downtime. This crucial step demands careful planning and execution, ensuring seamless communication and coordination between the palletizer and other systems. A well-integrated system allows for smooth material flow, optimized resource utilization, and reduced errors, ultimately contributing to a more productive and profitable operation.Integrating a palletizer isn’t just about connecting machines; it’s about harmonizing workflows and achieving a synergistic effect.
A flawlessly integrated system allows for real-time adjustments, predictive maintenance, and enhanced overall operational control. This meticulous integration effort is essential for realizing the full potential of the palletizer and optimizing the entire production process.
Key Factors in the Integration Process
The success of a palletizer integration hinges on several key factors. Careful consideration of these factors ensures a smooth transition and avoids potential pitfalls. Proper planning and thorough evaluation of these factors will yield the best results. These factors include the existing infrastructure, communication protocols, software compatibility, safety measures, and personnel training.
Communication Protocols
Effective communication is the cornerstone of a successful integration. The palletizer must communicate seamlessly with other systems in the production line, including conveyors, sorters, and control systems. This communication allows for precise timing, material flow, and data exchange, optimizing overall throughput. A critical component is the selection of appropriate communication protocols (e.g., Ethernet, PLC protocols) to ensure reliable data transfer.
For instance, a manufacturing facility using a real-time operating system (RTOS) for its automated systems should select a protocol that is compatible with the RTOS for optimal performance.
Role of Software and Automation
Software plays a pivotal role in managing the palletizer’s functions and integrating it with other systems. Software solutions typically include programming logic controllers (PLCs) for controlling the palletizer’s operations, as well as enterprise resource planning (ERP) systems for managing production data. Proper configuration and customization of these software components are critical for achieving efficient palletizing operations. This integration should ensure data consistency and provide real-time monitoring capabilities across all automated systems.
This ensures efficient tracking of materials, production status, and overall operational performance.
Infrastructure and Setup
The palletizer requires appropriate infrastructure to ensure proper operation. This includes power requirements, network connectivity, and adequate space for installation. The necessary electrical wiring, cabling, and mounting structures must be in place. Ensuring sufficient space for the palletizer’s components and surrounding equipment is critical for efficient workflow. Detailed blueprints and schematics for the installation process are vital for ensuring accuracy and minimizing downtime.
Safety Measures During Integration
Safety is paramount during the integration process. Safety procedures should be rigorously followed to prevent accidents. This includes proper guarding of moving parts, adherence to lockout/tagout procedures, and providing appropriate personal protective equipment (PPE) for personnel involved. Ensuring proper lighting, ventilation, and emergency shutdown mechanisms are essential. Safety training for all personnel involved in the integration process is critical to minimize risks.
Thorough risk assessments and the implementation of safety protocols are essential to ensure a safe working environment throughout the integration phase.
Integration Methods and Procedures
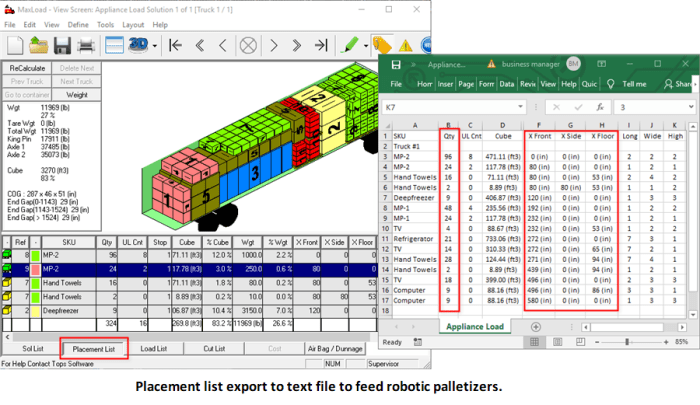
Mastering the integration of palletizers into your existing production line is a crucial step towards optimized efficiency and increased output. This process requires meticulous planning and execution, ensuring seamless communication and coordination between the palletizer and other equipment. The right integration method can dramatically reduce downtime and improve overall throughput.
Different Integration Methods
Various methods exist for integrating palletizers with existing systems. Direct integration, often employing custom-designed interfaces, offers the tightest control and highest level of performance. A phased approach, in contrast, allows for incremental integration, enabling the system to adapt as the production process evolves. Software-based integration, utilizing a common control system, facilitates flexibility and adaptability to future changes in production.
Each method has advantages and disadvantages based on the specific needs and resources of the production facility.
Steps in Palletizer Integration
Successful integration involves a structured approach. First, detailed planning is essential. This includes identifying the precise location for the palletizer, evaluating the existing infrastructure, and assessing the flow of materials through the production line. Second, installation and configuration must be executed meticulously. This includes verifying the palletizer’s functionality, calibrating the equipment, and connecting it to the relevant systems.
Third, rigorous testing and validation are crucial. Testing ensures that the palletizer functions as intended and seamlessly integrates with other equipment, and that the entire production line operates smoothly. Finally, comprehensive documentation, including operational procedures and troubleshooting guides, ensures smooth operation and efficient maintenance in the future.
Palletizer Configurations
Different configurations are possible for connecting the palletizer to other equipment. A typical setup might involve the palletizer receiving product directly from a conveyor system, a stacker crane to handle multiple product lines, or a robotic arm for handling products from various stations. The chosen configuration will depend on the specific layout of the production line and the nature of the products being handled.
For example, a fast-paced production line might require a direct conveyor connection, while a more complex system may benefit from a robotic arm to handle different product types. A well-designed configuration reduces bottlenecks and optimizes material flow.
Step-by-Step Integration Procedure
A standardized procedure for integration maximizes the likelihood of a successful implementation. First, create a detailed project plan, outlining timelines, responsibilities, and resource allocation. Second, meticulously document the existing production line and the specifications of the palletizer. Third, conduct a thorough site survey to identify potential integration challenges and ensure compatibility. Fourth, connect the palletizer to the appropriate power and data sources.
Fifth, carefully configure the palletizer’s parameters to match the specific requirements of the production line. Sixth, test the entire system rigorously to ensure seamless operation. Finally, develop comprehensive documentation and training materials for staff.
Troubleshooting Common Integration Issues
Integration problems can arise from mismatched equipment specifications, communication errors, or software conflicts. Troubleshooting requires a systematic approach. First, identify the source of the issue by checking the connection points, power supply, and communication channels. Second, review the system documentation and logs for error messages. Third, verify that the software configurations of the palletizer and other equipment are compatible.
Fourth, seek assistance from the equipment manufacturer’s support team if needed. A proactive approach to troubleshooting prevents prolonged downtime and minimizes disruption to the production process.
Software and Programming
Unlocking the full potential of your palletizer system hinges on robust software and meticulous programming. Mastering these elements empowers you to optimize performance, predict potential issues, and ensure flawless operation. This section delves into the crucial role of software in palletizer control, exploring the languages, configurations, and troubleshooting strategies that form the backbone of efficient palletizing.
Role of Software in Palletizer Control
Palletizer software acts as the central nervous system, orchestrating the entire process. It controls the movement of conveyors, the positioning of robotic arms, and the timing of product placement. Real-time monitoring capabilities allow operators to track progress, identify bottlenecks, and proactively address issues. Accurate data collection provides valuable insights for performance analysis and future improvements.
Programming Languages and Software
Various programming languages and software platforms are employed for palletizer control. Common choices include PLC programming languages like Ladder Logic, Structured Text, and Function Block Diagram, along with specialized palletizer control software from manufacturers. These platforms offer intuitive interfaces and robust functionalities for configuring and monitoring palletizer operations. Modern software often incorporates user-friendly graphical interfaces for easier setup and troubleshooting.
Basic Flowchart of a Palletizer Control System
A typical palletizer control system operates in a cyclical fashion, ensuring consistent and accurate product placement. The system starts by receiving product information, then evaluates the current pallet status. Based on this evaluation, the system sends instructions to the robotic arms and conveyors to place the product on the pallet. A final check verifies proper placement before moving to the next product.“`[Start] –> Product Information Input –> Pallet Status Evaluation –> Instruction Generation –> Robot/Conveyor Action –> Placement Verification –> [End] –> [Start]“`
Configuring Software for Specific Product Types
Software configuration is tailored to the specific characteristics of the products being palletized. Factors like product size, weight, and shape dictate the precise movement patterns and placement strategies employed by the palletizer. Careful calibration and adjustment are critical to ensure optimal handling and prevent damage to the products. Software provides parameters for adjusting the robotic arm’s reach, the conveyor’s speed, and the pallet’s orientation.
Common Software Errors and Resolution
Software errors can arise from various sources, including incorrect configuration settings, hardware malfunctions, or unforeseen product variations. Troubleshooting typically involves checking configuration files, reviewing logs for error messages, and performing diagnostics on the hardware. Common errors might include incorrect product dimensions, faulty sensor readings, or inadequate PLC communication. A systematic approach to identifying and resolving these issues is essential for maintaining efficient palletizer operation.
By understanding the software’s capabilities and limitations, operators can anticipate and resolve these problems proactively. Consult the manufacturer’s documentation and utilize online resources to identify and address the issue.
Safety and Compliance
Safe palletizer integration and operation are paramount. Prioritizing safety throughout the process, from initial design to ongoing maintenance, fosters a productive and secure work environment for everyone involved. This section delves into crucial safety standards and regulations, ensuring that the integration adheres to industry best practices and minimizes risks.Robust safety measures are not just a matter of compliance; they are fundamental to the long-term success and reliability of your palletizing system.
Implementing comprehensive safety protocols will protect personnel, equipment, and the overall workflow.
Safety Standards and Regulations, How to integrate palletizers
Adherence to relevant safety standards and regulations is critical for a safe palletizer integration. These regulations often encompass aspects like machine guarding, emergency stops, and operator training. Compliance with industry standards like OSHA (Occupational Safety and Health Administration) in the United States, or equivalent standards globally, ensures that the system meets minimum safety requirements. Failing to comply can lead to significant fines, and potentially more importantly, workplace accidents.
Design Considerations for Safe Operation
Palletizer design significantly influences its safety. Critical design elements include appropriate guarding around moving parts, ensuring adequate access for maintenance and operator intervention, and implementing redundant safety mechanisms. These measures prevent unintended contact with moving parts or malfunctions. The palletizer design should include a clear separation of operational zones from maintenance areas.
Importance of Operator Training
Comprehensive operator training is essential for safe palletizer operation. Operators must understand the machine’s functions, safety features, and procedures for proper use and maintenance. Training should cover identifying potential hazards, recognizing warning signs, and executing emergency procedures. Effective training minimizes the risk of accidents and ensures the operator can respond appropriately to unforeseen situations. This includes detailed instructions on the palletizer’s specific emergency shutdown procedures.
Procedures for Emergency Shutdowns
Clear and well-defined emergency shutdown procedures are crucial. These procedures must be readily accessible and clearly communicated to all personnel involved in the palletizer operation. Operators should be trained on the location and operation of emergency stop buttons, and the procedures to follow in case of malfunction or emergency. A visual indicator system to confirm the machine is completely stopped is also beneficial.
For example, a visual light that flashes when the machine is shut down.
Safety Equipment Needed During Integration and Operation
The use of appropriate safety equipment is mandatory during palletizer integration and ongoing operation. This includes personal protective equipment (PPE) like safety glasses, gloves, and appropriate footwear to protect against potential hazards. Other essential equipment may include fall protection systems, or specific respiratory equipment for certain tasks. Specific safety equipment is dependent on the palletizer design and the tasks involved during installation and operation.
Case Studies and Examples
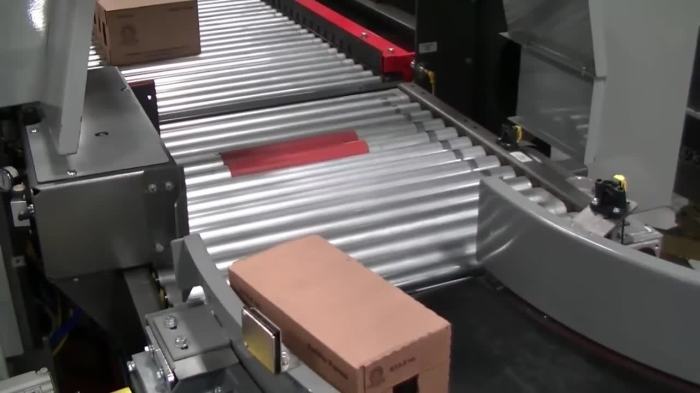
Successfully integrating palletizers requires careful planning and execution. Real-world case studies highlight the key factors for success and the potential pitfalls to avoid. These examples provide valuable insights into the integration process, from initial planning to final implementation and optimization. Understanding the challenges and triumphs of past integrations equips businesses with practical knowledge to navigate their own palletizer integration journeys.
Successful Palletizer Integrations in Various Industries
Numerous industries have successfully implemented palletizers, boosting efficiency and productivity. A food processing plant, for example, integrated a vertical palletizer to automate their packaging line. This streamlined their workflow, reduced labor costs, and improved product handling. Another example involves a logistics company that integrated a horizontal palletizer into their warehouse. This enhanced their order fulfillment process, allowing for faster and more accurate shipping.
The key to success in these integrations was meticulous planning, clear communication between the integrator and the client, and thorough testing of the entire system.
Challenges Faced During Integration
Integration projects are not without obstacles. One common challenge is the incompatibility of existing equipment with the new palletizer. This often necessitates modifications to the existing infrastructure, which can be time-consuming and costly. Another significant challenge is the lack of sufficient training for personnel on the new system. Proper training programs are crucial for successful operation and maintenance.
Finally, unforeseen technical issues can also delay or disrupt the integration process. These challenges, while common, can be mitigated through thorough planning, detailed system analysis, and robust communication throughout the integration process.
Types of Palletizers and Their Integration Methods
Different types of palletizers require unique integration strategies. Choosing the right method is essential for efficient operation and minimizing downtime.
Outcomes of Successful Integrations
Successful palletizer integrations yield significant benefits, including increased throughput, reduced labor costs, improved safety, and enhanced product quality. The streamlined workflow results in quicker order fulfillment and reduced handling errors.
Benefits of Integrating Palletizers
The integration of palletizers offers a multitude of benefits across various industries.
Future Trends in Palletizer Integration
The landscape of palletizer integration is constantly evolving, driven by technological advancements and the ever-increasing demands of modern logistics. This dynamic environment necessitates a proactive approach to understanding and adapting to these future trends. Integrating these advancements into existing palletizer systems will lead to enhanced efficiency, reduced operational costs, and improved overall productivity.The future of palletizer integration is inextricably linked with emerging technologies, demanding a proactive approach from businesses to maintain competitiveness.
Integrating these technologies into existing systems will result in streamlined operations, optimized resource utilization, and ultimately, increased profitability.
Emerging Technologies Influencing Integration
The integration of palletizers is increasingly being influenced by technologies like artificial intelligence (AI), machine learning (ML), the Internet of Things (IoT), and advanced robotics. These technologies are transforming how palletizers are controlled, monitored, and optimized, resulting in significant improvements in efficiency and safety.
Impact of AI and Machine Learning
AI and ML are poised to revolutionize palletizer integration by enabling predictive maintenance and dynamic optimization of palletizer operations. AI algorithms can analyze vast amounts of data from sensors and historical records to predict potential equipment failures, allowing for proactive maintenance schedules and minimizing downtime. Machine learning models can learn and adapt to changing production patterns, dynamically adjusting palletizer settings for optimal throughput and minimizing material handling errors.
For example, a palletizer equipped with AI could recognize variations in product sizes and weights, automatically adjusting its settings to maintain consistent pallet loads.
The Role of IoT in Real-Time Monitoring
IoT connectivity enables real-time monitoring and data collection from palletizers. This constant stream of data provides valuable insights into system performance, enabling predictive maintenance and process optimization. Sensors on palletizers can monitor factors like temperature, humidity, and vibration, helping to identify potential issues before they escalate. This continuous monitoring will allow for immediate identification of malfunctions, reducing downtime and optimizing resource allocation.
For instance, if a sensor detects excessive vibration, the system can alert operators, enabling prompt intervention and preventing potential damage.
Advanced Robotics and Automation
Advanced robotics are playing a crucial role in automating various aspects of palletizer integration. Collaborative robots (cobots) are particularly relevant, enabling safe and seamless integration with human operators. Cobots can handle tasks like loading and unloading products, freeing up human operators for higher-level tasks. This integration of robots with palletizers will enhance safety and reduce the risk of injury.
For instance, cobots can assist in picking and placing products on the palletizer, improving the overall speed and efficiency of the process.
Industry 4.0 and Palletizer Integration
The principles of Industry 4.0 are fundamentally changing how palletizers are integrated into production lines. Real-time data exchange between palletizers and other connected systems is crucial for optimizing the entire supply chain. This interconnectedness enables data-driven decision-making, allowing for dynamic adjustments to production schedules and resource allocation. Furthermore, Industry 4.0 concepts facilitate greater visibility and control over the entire palletizing process, leading to improved efficiency and reduced waste.
A factory utilizing Industry 4.0 principles could seamlessly integrate data from a palletizer with information from other production stages, optimizing the entire production process.
Outcome Summary
In conclusion, mastering palletizer integration is a crucial skill for modern manufacturers. This guide has equipped you with the knowledge to tackle the process, from initial planning to final implementation. By understanding the diverse factors involved – from system integration to safety compliance – you can confidently navigate the intricacies of this process. Remember, successful integration hinges on thorough planning, meticulous execution, and adherence to safety protocols.
Embrace these strategies, and you’ll unlock a new level of operational efficiency in your facility.
Clarifying Questions
What are the most common challenges encountered during palletizer integration?
Common integration challenges include compatibility issues between the palletizer and existing systems, communication protocol discrepancies, and unforeseen technical glitches. Careful planning, thorough testing, and proactive troubleshooting are essential to mitigate these risks.
How important is operator training in ensuring safe palletizer operation?
Operator training is paramount. Properly trained personnel are equipped to understand the safety protocols, machinery functions, and emergency procedures. This minimizes the risk of accidents and ensures consistent safe operation of the integrated system.
What software tools are typically used for palletizer control and monitoring?
Specific software used varies depending on the manufacturer and the complexity of the system. However, PLC programming, SCADA systems, and proprietary control software are commonly employed for real-time monitoring, control, and data analysis.
How do I determine the right palletizer type for my specific needs?
Consider factors such as the type of product, the volume of material, the space available, and the required speed of the process. Careful evaluation of these factors will help you select the most efficient and effective palletizer type.