How to install trailer wheel bearings is crucial for safety and longevity. Proper installation ensures smooth operation, preventing potential hazards and extending the life of your trailer. This comprehensive guide walks you through every step, from initial disassembly to final testing, ensuring a secure and reliable setup. We’ll explore the different bearing types, essential tools, and critical safety precautions.
This in-depth tutorial provides a detailed, step-by-step approach to installing trailer wheel bearings, addressing potential issues and emphasizing safety throughout the process. We’ll cover everything from preparing the trailer to testing the final assembly, ensuring a professional and safe outcome.
Introduction to Trailer Wheel Bearings
Trailer wheel bearings are the silent heroes of your trailer, ensuring smooth and safe operation. They support the weight of the trailer and its load, enabling effortless movement and reducing friction. Without proper functioning bearings, your trailer could experience significant issues, impacting both safety and longevity.Properly installed wheel bearings are critical for the safe and reliable performance of your trailer.
They minimize wear and tear, prevent premature failure, and ensure the smooth rotation of the wheels, leading to a much longer lifespan for your entire trailer. This is vital for safety, as a damaged or poorly installed bearing can result in a catastrophic failure, leading to potential accidents.
Types of Trailer Wheel Bearings
Trailer wheel bearings come in various designs, each suited to specific applications. Understanding the different types is key to selecting the correct bearings for your trailer and ensuring optimal performance. Common types include tapered roller bearings and ball bearings.
- Tapered Roller Bearings: These bearings are commonly used in trailers due to their ability to handle high loads and axial thrust. Their conical rollers allow for significant load-carrying capacity, making them ideal for heavy-duty trailers. They are known for their robustness and are well-suited for applications where the load is substantial.
- Ball Bearings: Ball bearings, though capable of supporting loads, often find application in lighter trailers or where the loads aren’t exceptionally high. Their smooth operation results in reduced friction, making them suitable for applications where minimal friction is preferred. Their lower cost often makes them an attractive option for less demanding applications.
Common Installation Issues
Incorrect installation of trailer wheel bearings can lead to a range of problems, impacting both safety and longevity. These issues can range from minor inconveniences to severe failures.
- Improper Lubrication: Insufficient or incorrect lubrication can lead to excessive friction, heat buildup, and premature wear of the bearing components. This can result in a noisy operation and eventually, bearing failure. Using the correct type and amount of grease is essential.
- Incorrect Bearing Preload: Insufficient or excessive preload can affect the bearing’s performance. Excessive preload can cause the bearing to overheat and fail prematurely. Insufficient preload can lead to excessive play and premature wear.
- Misaligned Bearings: Improper alignment of the bearings with the axle can cause uneven wear and tear on the components. This misalignment can cause a significant vibration and potentially damage the bearing or the axle.
- Damaged Bearing Housing: Damage to the bearing housing can compromise the integrity of the bearing assembly, leading to leaks and improper support. Ensure the housing is undamaged before installing the bearings.
Bearing Type, Application, and Installation Issues
The table below summarizes common bearing types, typical applications, and potential installation problems.
Bearing Type | Typical Application | Common Installation Issues |
---|---|---|
Tapered Roller | Heavy-duty trailers, cargo trailers, and utility trailers | Incorrect preload, misalignment, inadequate lubrication |
Ball Bearings | Light-duty trailers, utility trailers, and smaller trailers | Improper lubrication, insufficient preload, misalignment |
Tools and Materials Required

Getting your trailer’s wheel bearings installed properly is crucial for safety and longevity. The right tools and materials are paramount to a successful job, ensuring the bearings are installed correctly and securely. This section Artikels the essential equipment and lubricants needed, alongside vital safety precautions.
Essential Tools
A well-equipped toolbox is essential for this task. A variety of tools are required to dismantle, inspect, and reassemble the wheel bearing system. Improper tools can damage components, making the installation process more complex and potentially hazardous.
- Socket wrenches/ratchets: Various sizes are needed to remove and tighten fasteners, ensuring proper torque and preventing damage to the bearings or mounting hardware. Different sizes are necessary to accommodate the various bolts and nuts used in the trailer’s assembly.
- Torque wrench: Precise torque is critical for secure assembly. Incorrect torque can lead to premature failure or loosening of parts.
- Impact wrench (optional): Speeds up the process of removing and tightening fasteners, particularly in situations with multiple nuts and bolts.
- Bearing puller: Needed for safely removing and installing wheel bearings. This is often required due to the tight tolerances and sometimes stubborn nature of these components.
- Hammer and punches: Necessary for driving out and installing components.
- Measuring tools (e.g., calipers, micrometers): To ensure proper measurements of the bearings and the housing, guaranteeing a perfect fit.
- Cleaning supplies (e.g., compressed air, rags, solvent): Maintaining cleanliness throughout the process is vital. Dirt and debris can hinder proper lubrication and cause damage over time.
Lubricants
Proper lubrication is critical for the smooth operation and long life of the wheel bearings. The type of lubricant depends on the specific bearing type.
- Grease: Most common lubricant for trailer wheel bearings. The specific type of grease (e.g., lithium grease, moly grease) depends on the bearing design and the operating conditions. High-quality grease provides better protection against wear and corrosion.
- Wheel Bearing Lubricant: Specialized grease formulations designed for wheel bearings offer enhanced protection and performance. These are typically more resistant to water and other elements.
Safety Precautions
Safety is paramount during any installation procedure. Failure to follow safety precautions can result in injury or damage to the equipment.
- Wear appropriate personal protective equipment (PPE): Safety glasses, gloves, and sturdy footwear are essential to protect against potential hazards during the process.
- Work in a well-lit and ventilated area: This enhances visibility and prevents potential respiratory issues.
- Ensure the trailer is securely supported: Use jack stands or other appropriate support systems to prevent the trailer from tipping over.
- Disconnect the battery before working on electrical components: Prevents accidental electrical shocks.
- Use proper lifting techniques: Avoid straining your back or injuring yourself by using appropriate lifting techniques when handling heavy components.
Tool Summary
The following table summarizes the tools, their functions, and their importance in the trailer wheel bearing installation process.
Tool | Function | Importance |
---|---|---|
Socket wrenches/ratchets | Removing and tightening fasteners | Ensures secure assembly and prevents damage to components. |
Torque wrench | Applying precise torque to fasteners | Critical for secure assembly and prevents damage to bearings or mounting hardware. |
Impact wrench | Speeds up fastener removal/tightening | Increases efficiency, especially for multiple fasteners. |
Bearing puller | Removing and installing wheel bearings | Essential for safely handling bearings, preventing damage. |
Hammer and punches | Driving out and installing components | Enables the removal and installation of components, often necessary for bearing replacement. |
Measuring tools | Ensuring accurate measurements | Guarantees a proper fit and prevents issues with tolerances. |
Cleaning supplies | Maintaining cleanliness | Prevents contamination and ensures proper lubrication. |
Preparing the Trailer for Installation
Getting your trailer’s wheel bearings ready for replacement is a crucial step. A well-prepared trailer ensures a smooth installation process and a longer lifespan for the new bearings. This section details the disassembly procedure, damage inspection, and necessary cleaning steps, all critical for a successful job.Properly preparing the trailer involves meticulous disassembly of the old bearings, careful inspection for damage, and thorough cleaning to ensure the new bearings are installed in optimal conditions.
This meticulous approach prevents complications and maximizes the new bearings’ performance.
Disassembling the Old Wheel Bearings
The disassembly process involves systematic steps to remove the old bearings without damaging the axle or frame. Care and attention to detail are paramount throughout this procedure. Incorrect handling can lead to costly repairs or the need for replacements in the future.
- Secure the Trailer: Park the trailer on a level surface and engage the parking brake. This prevents any accidental movement during the process.
- Remove the Wheel: Loosen and remove the lug nuts from the wheel. Carefully lift and remove the wheel. Note the specific orientation of the wheel for reassembly.
- Release the Hub: Carefully release the retaining clips or cotter pins that hold the hub in place. If present, remove any dust caps or shields.
- Disconnect the Hub: Carefully separate the hub from the axle, ensuring you don’t damage the threads or the hub’s mounting surface.
- Remove the Bearings: Use the appropriate bearing pullers to carefully remove the bearings from the axle and races. If you do not have the correct tools, seek professional help.
Inspecting the Trailer Frame and Axle
A thorough inspection of the trailer frame and axle for damage is critical. Any damage can lead to issues during the installation process and the long-term performance of the new bearings. Take your time and be thorough.
- Visual Inspection: Carefully examine the axle and frame for any signs of cracks, bends, or corrosion. Pay attention to areas around the bearing races and the axle itself. Look for any irregularities.
- Check for Wear: Assess the condition of the bearing races. Significant wear or damage will affect the new bearing’s performance and longevity. Note any imperfections.
- Assess the Frame: Examine the frame’s structural integrity. Ensure there are no cracks, dents, or other damage that could compromise the support or alignment.
- Document Findings: Carefully document any observed damage. This documentation will be helpful if you need to address any issues during installation.
Removing the Old Bearings Carefully
Removing the old bearings safely and without causing damage is vital. The right tools and procedures prevent future issues and maintain the integrity of the axle and frame.
Steps | Actions | Safety Considerations |
---|---|---|
1 | Use appropriate bearing pullers to remove the bearings. | Ensure the puller is properly fitted to avoid damaging the axle or bearings. |
2 | If using a hammer, use gentle taps and avoid striking the axle directly. | Incorrect hammering can lead to deformation of the axle. |
3 | Apply pressure evenly when using bearing pullers. | Uneven pressure can lead to the bearing being damaged. |
4 | Inspect the axle and bearing races for damage after removing the bearings. | Identify any damage that may require further attention or replacement. |
Cleaning the Axle and Bearing Races
Cleaning the axle and bearing races is essential to ensure proper lubrication and function of the new bearings.
- Thoroughly clean the axle and bearing races with a suitable degreaser and a brush. Remove any dirt, rust, or debris.
- Use compressed air or a clean cloth to remove any remaining debris. Pay close attention to the bearing races and ensure they are clean and free of any foreign objects.
- Inspect the cleaned parts for any imperfections or signs of damage.
Clean Working Area and Lubrication
Maintaining a clean working area and following proper lubrication procedures is critical for the longevity of the new bearings. A clean workspace minimizes contamination, ensuring proper function and reducing the risk of premature wear.
- Cleanliness: Ensure the work area is clean and free of debris. This prevents contamination of the new bearings.
- Lubrication: Use the appropriate lubricant specified by the bearing manufacturer for the new bearings. Follow the manufacturer’s instructions carefully. Using the correct lubricant prevents friction and wear.
Installing the New Bearings
Installing new trailer wheel bearings is a critical step in ensuring the safety and longevity of your trailer. Proper installation is paramount for smooth operation, preventing premature wear, and avoiding potential accidents. Careful attention to detail and adherence to the manufacturer’s recommendations are essential throughout this process.
Installing the New Bearings: A Step-by-Step Guide
This section provides a detailed procedure for installing new bearings, emphasizing crucial steps and potential issues. Following these instructions precisely will significantly increase the chances of a successful and safe installation.
Step Number | Procedure | Potential Issues |
---|---|---|
1 | Carefully inspect the new bearings. Ensure they are free from damage, such as dents, cracks, or other imperfections. Check for any visible manufacturing defects. | Damaged bearings should not be used. Discard them immediately and replace them with new, undamaged bearings. |
2 | Clean the bearing race surfaces on the axle and the bearing housing. Remove any rust, dirt, or debris. Use a suitable degreaser and a clean cloth or brush for thorough cleaning. | Inadequate cleaning can lead to poor lubrication and premature bearing failure. Ensure complete removal of contaminants. |
3 | Install the bearings into the housing. Ensure the bearings are properly aligned and seated. The bearing races should be smooth and free from obstructions. Use appropriate lubricant on the inner race of the bearing and on the contact surface of the bearing. | Misaligned bearings may cause uneven wear or binding. Verify the bearings’ alignment with the housing and the axle. |
4 | Apply the correct preload. This is crucial for proper bearing function. The preload ensures the bearings are properly compressed against the races, preventing excessive play. Consult the manufacturer’s specifications for the precise amount of preload. | Insufficient preload may result in excessive play and noise, while excessive preload can cause damage to the bearings. Use a torque wrench to apply the correct preload. |
5 | Ensure the bearings are fully seated on the axle. This ensures that the bearings are correctly positioned and will operate smoothly. Check for any signs of binding or misalignment. | Incorrect seating may cause uneven load distribution, leading to premature failure. Verify the bearing is firmly in place against the axle. |
6 | Lubricate the bearings with the appropriate grease. Apply a generous amount of grease to the bearing’s inner and outer races. Use a grease fitting if available. This ensures the bearings receive the proper lubrication throughout their lifespan. Avoid over-greasing. | Insufficient lubrication can lead to friction and rapid wear, while excessive lubrication can lead to contamination and leakage. Follow manufacturer recommendations. |
7 | Tighten the bearing caps using a torque wrench. Tighten the caps to the specified torque value. Tightening too much can damage the bearings or the housing. Tightening too little can allow the bearings to become loose. | Incorrect tightening torque can cause bearing damage or improper bearing function. Always use a torque wrench to maintain the correct tightening value. |
Importance of Preload
Proper preload is essential for the smooth and efficient operation of wheel bearings. It ensures that the bearings are properly compressed against the races, preventing excessive play. Insufficient preload can result in noise and vibration, while excessive preload can lead to bearing damage. Always follow the manufacturer’s specifications for the appropriate preload.
Correct preload ensures a balance between smooth operation and adequate support for the load.
Reassembling the Trailer: How To Install Trailer Wheel Bearings
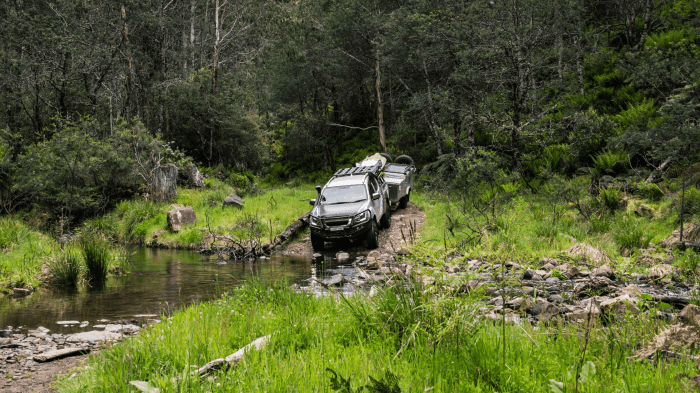
Putting your trailer back together is crucial for its safe and proper function. Incorrect reassembly can lead to misalignment, braking issues, and even accidents. Thoroughness and attention to detail are paramount during this phase.
Reassembling Trailer Components
Carefully placing each part back in its designated spot ensures the trailer’s structural integrity. This includes attaching all hardware, securing connections, and aligning components accurately. A methodical approach minimizes the risk of errors and maximizes the trailer’s longevity.
Wheel and Axle Alignment
Precise alignment of the wheels and axle is vital for safe operation. Incorrect alignment can lead to uneven tire wear, steering difficulties, and compromised handling. The correct alignment ensures the trailer tracks straight and responds predictably to steering inputs. Using a straight edge or a level to check for any misalignment is essential.
Checking Wheel Alignment
Verifying wheel alignment is a critical step. Misaligned wheels can result in uneven tire wear and a tendency to pull to one side. This can lead to safety issues and premature tire failure. A properly aligned wheel set ensures the trailer tracks straight and minimizes tire wear. Use a straight edge or a level to check for alignment.
Reconnecting Brake Lines and Components
Reconnecting brake lines and other components requires meticulous attention to detail. Improperly connected brake lines can compromise braking performance and lead to dangerous situations. Correctly reconnecting components is crucial for the trailer’s overall safety and performance. Ensure all connections are tight and secure.
Checking Wheel Bearing Rotation
Checking the wheel bearings for smooth rotation is a critical step in ensuring the trailer’s smooth operation and safety. Rough or noisy rotation indicates a potential issue with the bearings, requiring further investigation and repair. A smooth, quiet rotation is a sign of properly installed and functioning wheel bearings. Using your hands to feel for any unusual resistance or noise is a good initial test.
Reassembly Steps Table
Step | Component | Potential Issues |
---|---|---|
1 | Axle assembly | Misalignment, loose bolts, damage to the axle assembly |
2 | Wheel bearings | Incorrect installation, damage to the bearings, improper lubrication |
3 | Wheels | Bent rims, misalignment, damage to the wheel structure |
4 | Brake lines | Leaking lines, disconnected fittings, damage to the lines |
5 | Hub caps and hardware | Loose caps, damaged hardware, incorrect tightening |
6 | Suspension components (if applicable) | Loose or damaged suspension components, incorrect installation |
7 | Trailer frame | Damage to the frame, loose or missing welds, structural issues |
Testing and Verification
Installing new trailer wheel bearings is a crucial step, but it’s not complete without thorough testing. Proper functionality and safety are paramount. This section details the critical steps for verifying the installation’s success. Correctly functioning bearings and alignment ensure the trailer’s safe operation on the road.
Thorough Bearing Test
This step ensures the bearings rotate smoothly and without excessive play. It’s essential to identify any potential issues early to prevent costly repairs down the road. Failure to perform this test could lead to unexpected breakdowns or safety hazards.
- Visual Inspection: Carefully examine the bearings for any signs of damage, such as cracks, dents, or excessive wear. Look for any foreign objects trapped within the bearing assembly. Visual inspection should be performed before any rotation testing.
- Rotation Test: Rotate each wheel by hand to assess smooth rotation. Listen for any grinding, clicking, or unusual noises. Excessive resistance or unusual noises indicate potential problems that need immediate attention.
- Load Test (Optional): If possible, apply a moderate load to the trailer’s axle to simulate real-world conditions. This helps in identifying any issues that may only become apparent under load. Observe for any changes in the bearings’ operation.
Checking Wheel Bearing Play
Correct wheel bearing play is crucial for smooth operation and longevity. Incorrect play can lead to premature wear, noisy operation, and potential safety issues.
- Using a Dial Indicator: Place the dial indicator on the wheel hub. Ensure the indicator is correctly positioned to measure the radial play.
- Measuring Play: Rotate the wheel slowly, and observe the indicator readings. The acceptable play will vary depending on the specific bearing specifications. Refer to the manufacturer’s guidelines for the precise range.
- Interpreting Results: If the measured play exceeds the acceptable range, it indicates a problem with the bearings or the wheel hub. Address the issue before proceeding with further steps.
Ensuring Proper Wheel Alignment
Accurate wheel alignment ensures the trailer’s stability and handling. Incorrect alignment can lead to uneven tire wear, increased fuel consumption, and potentially hazardous situations.
- Using a Straight Edge: Place a straight edge across the top of the tires. Visualize the straight line and compare it with the tires. Any deviation indicates misalignment.
- Checking with a Level: Use a level to ensure the trailer is level and stable. This will help you determine if the wheels are aligned correctly.
- Adjustments (if necessary): If misalignment is detected, adjust the trailer’s suspension or other relevant components according to the manufacturer’s instructions. Ensure that the alignment is checked again after any adjustments.
Verifying Brake Function, How to install trailer wheel bearings
Functional brakes are critical for the trailer’s safety. Proper brake operation prevents accidents and ensures the trailer’s stability under various conditions.
- Applying Brakes: Apply the brakes and ensure they engage properly. Listen for the expected braking sound.
- Testing Brake Performance: Test the brakes under various load conditions, if possible. Check if the brakes are responsive and provide adequate stopping power.
- Checking Brake Pads: Inspect brake pads for wear. If necessary, replace them according to the manufacturer’s guidelines.
Safety Checks Before Operation
Comprehensive safety checks are essential before operating the trailer. These checks ensure the trailer is roadworthy and free from potential hazards.
- Visual Inspection: Check for any visible damage or loose parts on the trailer.
- Wheel Integrity: Inspect the wheels for any signs of damage, such as cracks or loose fasteners.
- Lighting Function: Ensure all lights, including brake lights, turn signals, and taillights, are functioning correctly.
Troubleshooting Flowchart
A flowchart, although not displayed here, would visually illustrate the testing process, with branches for troubleshooting different potential issues. The flowchart would show the steps to take for various scenarios, such as excessive play, unusual noises, or brake malfunctions. This would guide the user through the necessary steps to identify and resolve any issues.
Troubleshooting Common Issues
Installing trailer wheel bearings can be tricky, and unexpected problems can arise. Knowing how to identify and address these issues quickly and efficiently is crucial for a successful installation and the long-term performance of your trailer. This section Artikels common problems and their solutions to help you navigate potential pitfalls.
Identifying Excessive Play
Excessive play in the bearings can manifest as a noticeable wobble or looseness in the wheel assembly. This can be a significant safety concern and often indicates a problem with the bearings or the surrounding components. Diagnosing this involves careful inspection and testing. First, visually assess the wheel for any misalignment or damage. Then, gently rock the wheel.
If there’s excessive movement, the bearings need further examination.
Diagnosing Noise Issues
Unusual noises during operation can be indicative of bearing issues. These sounds might range from grinding or screeching to a high-pitched whine. Identifying the source of the noise is essential. Start by carefully listening for the sound, noting its characteristics (pitch, intensity, rhythm). The sound’s location on the wheel assembly can help pinpoint the problematic area.
For instance, a constant high-pitched whine could suggest worn bearings, while a grinding sound could indicate damaged races or other parts.
Addressing Bearing Wear
If the bearings exhibit excessive wear or damage, they must be replaced. Worn bearings often result in excessive play and noise. Proper lubrication is also crucial for the longevity of the bearings. Use the recommended lubricant for the specific bearing type and ensure adequate lubrication to prevent further wear and potential damage.
Common Causes and Solutions
- Problem: Wheel misalignment. Solution: Check and adjust the wheel alignment before installing new bearings. Improper alignment can cause the bearings to experience excessive stress, leading to premature wear and potential damage.
- Problem: Incorrect bearing installation. Solution: Ensure the bearings are installed in the correct orientation and with the proper amount of preload. Misalignment or improper preload can lead to excessive play and noise. Refer to the manufacturer’s specifications for detailed installation procedures. Consult the user manual or online resources for proper orientation and preload instructions.
- Problem: Insufficient lubrication. Solution: Use the correct amount and type of grease or lubricant specified by the manufacturer. Ensure proper lubrication throughout the bearing assembly to prevent friction and heat buildup. Insufficient lubrication will lead to increased friction and accelerated wear.
- Problem: Damaged races or inner/outer rings. Solution: If the races or rings are damaged, replace them. Damaged races or rings cannot support the bearings correctly, leading to premature wear and potential failure.
- Problem: Incorrect preload. Solution: Apply the correct amount of preload to the bearings. Over-tightening can cause the bearings to fail prematurely. Under-tightening will lead to excessive play.
Addressing Installation Issues
Installation issues can stem from improper procedures or faulty components. Following the manufacturer’s guidelines and using appropriate tools is paramount. A detailed checklist, covering every step of the process, can be very useful in identifying any potential problems.
- Problem: Difficulty installing the bearings. Solution: Ensure the bearings are properly seated and not binding. Check the installation process for any missed steps or inconsistencies.
- Problem: Incorrect tool usage. Solution: Utilize the correct tools and techniques for handling the bearings. Incorrect tools or force can damage the bearings.
- Problem: Missing or damaged components. Solution: Thoroughly inspect all components before starting the installation. Any missing or damaged parts must be replaced immediately. Double-checking all parts before installation helps prevent unexpected problems.
Conclusion
In conclusion, mastering trailer wheel bearing installation empowers you to maintain your trailer in optimal condition. By following these detailed steps, you’ll not only ensure safety but also extend the life of your trailer and its components. Remember, proper installation is paramount to preventing costly repairs and maintaining the integrity of your vehicle. Always prioritize safety and consult resources for further clarification if needed.
User Queries
What lubricant should I use for tapered roller bearings?
Consult the manufacturer’s recommendations for the specific lubricant type and viscosity suitable for your bearing type. Using the correct lubricant is crucial for proper lubrication and performance.
How can I tell if my axle is damaged?
Visually inspect the axle for any cracks, bends, or signs of distortion. Feel for any unusual looseness or play in the axle. If you suspect damage, consult a professional mechanic before proceeding with the installation.
What are the typical signs of improperly installed wheel bearings?
Excessive noise, vibration, or play in the wheel bearings are clear indicators of improper installation. Uneven wheel rotation and difficulty in turning the wheels are also potential problems.
How much preload is necessary for ball bearings?
The precise amount of preload for ball bearings varies depending on the specific bearing type and manufacturer’s specifications. Always refer to the manufacturer’s instructions or a reputable guide for accurate preload information.