How long to pull vacuum on car AC system is a critical aspect of maintaining optimal performance. The duration varies significantly based on vehicle type, refrigerant type, and the condition of the AC system. Understanding these factors is crucial for efficient and effective service.
This analysis examines the intricacies of the vacuuming process, from the influencing factors to the best practices and troubleshooting steps. A comprehensive understanding of these elements is essential for technicians and DIY enthusiasts alike to ensure a successful AC system repair or maintenance procedure.
Vacuuming Time Variations
The optimal vacuuming time for a car’s air conditioning (AC) system is crucial for effective system performance and longevity. Variations in vacuuming times are influenced by numerous factors, including vehicle type, refrigerant type, and the system’s condition. Precise evacuation ensures efficient refrigerant flow and proper system operation.Accurate vacuuming times are essential to remove air and moisture from the AC system.
Insufficient evacuation can lead to reduced efficiency and potential compressor damage, while over-evacuation can lead to difficulties in achieving a proper refrigerant charge. Establishing a range of appropriate vacuuming times for various situations allows technicians to optimize the process and achieve the desired outcomes.
Typical Vacuuming Time Ranges
Determining the precise vacuuming time for a car’s AC system necessitates consideration of various factors. Different vehicle makes and models, and their specific AC system configurations, can influence the duration of the process. The following table provides a general guideline for typical vacuuming time ranges.
Vehicle Type | Typical Vacuuming Time Range (minutes) | Factors Affecting Time |
---|---|---|
Small Cars (e.g., subcompacts) | 20-30 | Smaller refrigerant charge, simpler system design. |
Mid-size Sedans | 25-40 | Intermediate system complexity, moderate refrigerant charge. |
SUVs and Trucks | 30-50 | Larger refrigerant charge, more complex system design, potential for larger leak areas. |
Luxury Vehicles | 35-55 | Potentially complex system designs, larger refrigerant charge, potentially more intricate leak areas. |
The listed times are approximate guidelines and may vary based on the specific vehicle’s AC system configuration and the presence of leaks or previous repairs.
Impact of Refrigerant Type
The type of refrigerant used in the car’s AC system significantly impacts the vacuuming process. Different refrigerants have varying vapor pressures and boiling points, affecting the rate at which air and moisture are removed. For instance, the vacuuming time for systems using R-134a may differ from those using R-1234yf.Different refrigerants require different procedures to ensure complete evacuation. This may involve adjustments to the vacuum pump’s settings and potential modifications to the overall vacuuming process.
Effect of System Condition
The condition of the car’s AC system plays a crucial role in determining the vacuuming time. Leaks in the system, whether small or large, directly impact the amount of air and moisture that need to be removed. Previous repairs, such as compressor replacements or refrigerant line repairs, can also affect the time required for adequate evacuation.Systems with leaks will require longer vacuuming times, as the leaks can introduce air and moisture into the system.
The severity of the leaks will influence the time needed for proper evacuation. Systems with previous repairs may need a thorough inspection before vacuuming to identify any potential additional leaks or obstructions that could hinder the evacuation process.
Methods for Determining Adequate Evacuation
Several methods can be used to determine when the AC system has been adequately evacuated. The most common method involves using a vacuum gauge to monitor the pressure inside the system. The gauge reading should reach a predetermined vacuum level, typically in the range of 250-290 microns of mercury (Hg).
Vacuum gauges are crucial for monitoring the evacuation process and ensuring a consistent vacuum level.
Other methods include observing the system for any signs of residual air, such as hissing sounds or bubbling. Thorough checks should also include inspecting the refrigerant lines for any leaks, as the vacuum gauge reading may not accurately reflect the presence of hidden leaks.
Factors Affecting Vacuuming Duration
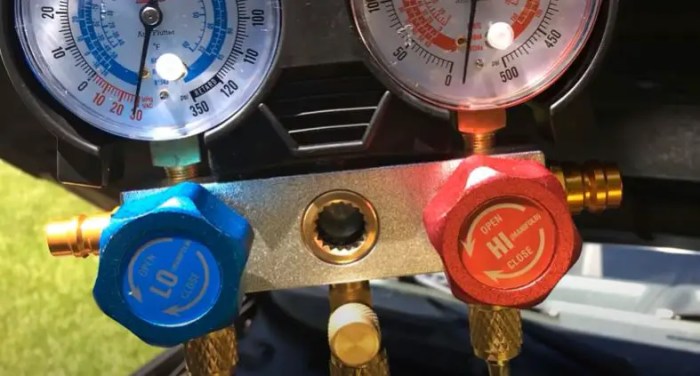
The process of evacuating air from a car’s air conditioning (AC) system, known as vacuuming, is crucial for removing moisture and air pockets. The duration of this process is not fixed and depends on several factors. Understanding these factors is essential for technicians to optimize the AC system’s performance and efficiency.The effectiveness and duration of the vacuuming process are influenced by various conditions within the system.
Moisture, air leaks, and the pump’s capabilities all play a role in determining how long it takes to achieve the desired vacuum level. Different pump types also affect the vacuuming time, as do the system’s characteristics.
Moisture Content
The presence of moisture significantly impacts vacuuming time. Water molecules, trapped within the AC system’s components, present a barrier to achieving a thorough vacuum. This is because water vapor requires time to be removed. Moisture interferes with the vacuum process by reducing the system’s ability to achieve a low pressure. Removing moisture effectively is crucial for preventing future problems.
Air Leaks
Air leaks are another critical factor influencing vacuuming time. Even small leaks can prevent the system from reaching a sufficient vacuum. These leaks allow air to re-enter the system, negating the effect of the vacuum pump. Finding and sealing these leaks is essential for achieving a thorough vacuum. Leaks can be present in hoses, seals, or fittings.
Vacuum Pump Specifications
The specifications of the vacuum pump used directly correlate with the vacuuming time. A higher CFM (cubic feet per minute) rating indicates a higher pumping capacity. A pump with a higher CFM will evacuate the system faster. For example, a pump with a 100 CFM rating will typically remove air faster than a pump with a 50 CFM rating, resulting in a shorter vacuuming time.
This is because the higher CFM pump can remove more air volume per unit of time.
Vacuum Pump Type
Different types of vacuum pumps have varying efficiencies in achieving and maintaining a vacuum. Rotary vane pumps are commonly used in automotive AC systems. These pumps are relatively efficient and effective for most applications. However, other pump types, such as scroll pumps, may have different performance characteristics, affecting the vacuuming time. The specific pump type can influence the speed at which the system reaches the desired vacuum pressure.
Comparison of Factors Affecting Vacuuming Time
Factor | Description | Impact on Vacuuming Time |
---|---|---|
Moisture Content | Presence of water vapor in the system | Increased vacuuming time; requires additional time to remove moisture. |
Air Leaks | Breaches in the system’s integrity | Significantly increased vacuuming time; prolonged time to reach vacuum pressure. |
Vacuum Pump CFM | Pump’s air displacement capacity | Higher CFM results in faster vacuuming time. |
Vacuum Pump Type | Specific pump design | Different pump types may have varying efficiency; may impact vacuuming time. |
Procedure for Vacuuming
Proper vacuuming of a car’s air conditioning (AC) system is crucial for ensuring optimal performance and longevity. A thorough vacuum removes moisture, air, and other contaminants, creating a dry, clean environment conducive to efficient refrigerant flow and preventing the formation of harmful contaminants that can damage the system over time. This process is critical for effective AC system maintenance.
Vacuuming Procedure
The following procedure Artikels a systematic approach to vacuuming a car’s AC system. Adherence to this step-by-step process is essential for achieving a successful and safe vacuuming operation.
- Preparation and Safety: Ensure the vehicle’s engine is off and the AC system is completely shut down. Disconnect the battery terminals to prevent accidental electrical shocks. Wear appropriate personal protective equipment (PPE), including safety glasses, gloves, and a long-sleeved shirt, to protect against potential hazards. Ensure the work area is well-ventilated.
- System Isolation: Identify and disconnect all components connected to the AC system, including the condenser, evaporator, compressor, and drier. This step prevents the accidental release of refrigerant and ensures that the system is properly isolated from other vehicle systems. Thorough isolation is critical to avoid unintended consequences and maintain safe working conditions.
- Vacuum Pump Connection: Connect the vacuum pump to the designated ports on the AC system. This ensures a proper connection between the vacuum pump and the AC system. Using a vacuum gauge, monitor the vacuum level throughout the process. Use a correct vacuum gauge and proper vacuum pump connections to maintain accuracy.
- Vacuuming Process: Initiate the vacuum pump and monitor the vacuum level using the vacuum gauge. The vacuum level should ideally reach and maintain a reading of at least 290 microns (290×10 -6 mmHg) or higher. Maintain the vacuum for a predetermined time period, typically ranging from 30 minutes to 2 hours. This ensures complete removal of contaminants and creates a clean environment within the system.
- System Leak Detection: After the vacuuming process, perform a leak check on the system. If any leaks are detected, repair them immediately to prevent refrigerant loss. Leaks can significantly impact the system’s performance and require careful attention to identify and repair.
- System Recharge: Once the system is leak-free and the vacuum is maintained, recharge the AC system with the correct type and amount of refrigerant. Follow the manufacturer’s specifications for proper refrigerant type and quantity. Failure to follow these specifications can lead to performance issues and potential damage to the AC system.
- System Verification: After recharging, verify the AC system’s functionality by testing the cooling output. This step ensures the AC system operates correctly. Proper verification confirms the efficiency of the vacuuming process and the recharging procedure.
Step Number | Action | Rationale |
---|---|---|
1 | Preparation and Safety | Ensures safety and proper system isolation. |
2 | System Isolation | Prevents refrigerant release and ensures proper isolation. |
3 | Vacuum Pump Connection | Establishes connection for vacuuming process. |
4 | Vacuuming Process | Removes contaminants and creates a clean environment. |
5 | System Leak Detection | Identifies and repairs potential leaks for optimal performance. |
6 | System Recharge | Ensures the system is fully functional. |
7 | System Verification | Confirms the efficiency of the process. |
Troubleshooting Vacuuming Issues
Vacuuming a vehicle’s air conditioning system is a critical step in ensuring proper system function. Failure to achieve a sufficient vacuum can indicate leaks, impacting the efficiency and longevity of the refrigerant charge. Identifying and resolving vacuuming issues promptly is essential to avoid unnecessary repair costs and ensure a properly functioning AC system.
Potential Problems Prolonging Vacuuming
Various factors can contribute to prolonged vacuuming times, necessitating careful examination. Inaccurate or incomplete leak detection is a frequent culprit. Poorly sealed connections, damaged hoses, or overlooked fittings can all contribute to leaks, requiring extensive time for re-evacuation. Furthermore, the presence of air pockets, trapped moisture, or insufficient pumping capacity of the vacuum pump can hinder the attainment of a sufficient vacuum.
Causes of Extended Vacuuming Times
- Leaks in the System: Leaks, no matter how small, impede achieving a satisfactory vacuum. A significant leak will prevent the vacuum pump from creating a sufficiently low pressure to maintain the vacuum. This can result from damaged hoses, fittings, or seals. Proper leak detection is crucial in determining the location and extent of leaks. For example, a small leak in a hard-to-reach area might take considerably longer to identify and repair, leading to prolonged vacuuming.
- Air Pockets and Moisture: Air pockets trapped within the system can prevent the vacuum pump from drawing a sufficient vacuum. Moisture, often from condensation, can also hinder the process. These issues require purging the system of air and moisture before vacuuming. The use of moisture absorbers or a dedicated drying process is often necessary.
- Insufficient Vacuum Pump Capacity: An inadequate vacuum pump might struggle to achieve the necessary low pressure. This can be due to wear and tear, or the pump might not be compatible with the system’s size or complexity. Upgrading or replacing the vacuum pump can significantly reduce vacuuming time.
- Improper Vacuuming Procedure: Inaccurate procedure, such as failing to adequately purge the system of air or moisture, or incorrectly using the vacuum pump, can lead to significant vacuuming time delays. Following a standardized procedure, with thorough checks at each step, is crucial to avoid these issues.
Vacuum Pump Troubleshooting
- Pump Malfunction: If the vacuum pump is not achieving the expected vacuum pressure, it might be malfunctioning. Common issues include a worn-out pump, a faulty motor, or a clogged filter. Checking the pump’s operation and ensuring its compatibility with the AC system are vital. Diagnostic tools and specialist inspection can help pinpoint the problem.
- Electrical Issues: Problems with the electrical supply to the vacuum pump can also impact its performance. Checking the power source, fuses, and wiring connections for any damage or issues can resolve these problems. Ensuring the pump receives adequate voltage is crucial.
- Vacuum Gauge Issues: A malfunctioning vacuum gauge can lead to inaccurate readings, potentially delaying the vacuuming process. Checking the gauge’s accuracy and ensuring proper calibration is essential. Using a reliable, calibrated vacuum gauge is essential for accurate readings.
Significance of Leak Detection
Proper leak detection is crucial for efficient and accurate vacuuming.
Identifying and repairing leaks before initiating the vacuuming process is essential. A leak, no matter how small, significantly impacts the vacuuming time, as the vacuum pump will continuously work to maintain the vacuum, but the leak will quickly dissipate the vacuum. Thorough leak detection using methods like dye tracing, electronic leak detectors, or manifold pressure readings can accurately identify the location and size of leaks, thus improving the efficiency and accuracy of the entire AC service process.
Early detection and repair of leaks significantly reduce the overall time required to vacuum the system.
Vacuuming Time Best Practices
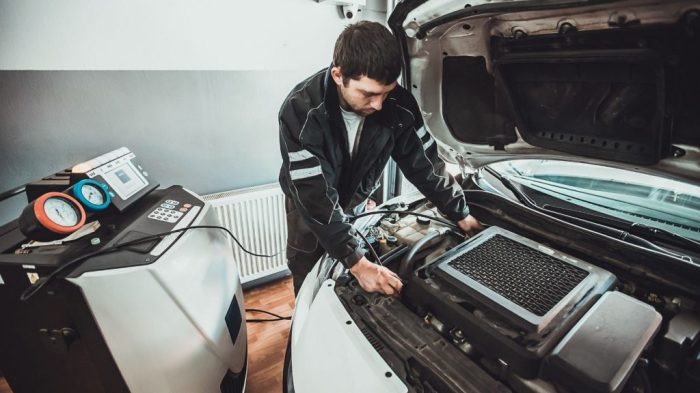
Optimal vacuuming time for a car’s AC system hinges on thoroughness and adherence to established procedures. Achieving a complete vacuum is crucial for effective system performance and longevity, preventing moisture from accumulating and hindering proper refrigerant flow. Consistent adherence to best practices minimizes potential issues and ensures the AC system functions as intended.Accurate vacuum readings are vital for determining the system’s readiness for refrigerant charging.
The process demands meticulous attention to detail, from initial system preparation to final gauge verification. This ensures that the system is properly evacuated and ready for the introduction of fresh refrigerant.
Importance of Thoroughness
Thoroughness in the vacuuming process is paramount. Incomplete evacuation can lead to the presence of residual air or moisture within the system. This residual contamination compromises the system’s efficiency and ultimately reduces the longevity of the AC unit. A thorough evacuation is the foundation for a properly functioning AC system, enabling optimal refrigerant charge and cooling performance.
Attention to Detail in the Vacuuming Process
Meticulous attention to detail throughout the vacuuming procedure is essential for a successful outcome. This includes ensuring all connections are secure, checking for leaks in the system, and verifying the integrity of the vacuum pump. Paying attention to potential leaks prevents the loss of vacuum and the subsequent introduction of contaminants.
Common Mistakes to Avoid
- Insufficient vacuum time: Insufficient vacuum time allows residual air or moisture to remain in the system, impacting the system’s efficiency and potentially leading to premature failure.
- Inadequate system preparation: Failing to properly prepare the system, such as checking for leaks or ensuring proper connections, can result in inconsistent or incomplete vacuuming.
- Ignoring gauge readings: Ignoring or misinterpreting gauge readings during the vacuuming process can lead to inaccurate estimations of the system’s vacuum level, potentially leading to incorrect refrigerant charges.
- Using an inadequate vacuum pump: A vacuum pump that is not capable of generating sufficient vacuum levels will result in an incomplete evacuation of the system.
Correct Gauge Readings and Their Impact, How long to pull vacuum on car ac system
Accurate gauge readings are critical for determining the effectiveness of the vacuum process. A reading of 29.92 inches of mercury (Hg) or better is generally considered a satisfactory level for a complete vacuum. Fluctuations or lower readings indicate incomplete evacuation and the presence of air or moisture within the system.
- Maintaining consistent readings: Consistent readings throughout the vacuuming process are a key indicator of a stable vacuum level. Any fluctuations may point to leaks or incomplete evacuation.
- Understanding gauge limitations: Understanding the limitations of the pressure gauges used in the process is crucial. Using a gauge beyond its intended range can lead to inaccurate readings.
- Gauge accuracy validation: Periodically validating the accuracy of the pressure gauges is essential to ensure reliable readings. Calibration ensures the readings accurately reflect the vacuum levels.
Vacuuming Time for Different AC System Components: How Long To Pull Vacuum On Car Ac System
Accurate vacuuming time for an automotive air conditioning (AC) system is crucial for effective system recovery. Precisely determining the time needed for each component, considering factors like size and complexity, allows technicians to efficiently diagnose and address issues, minimizing downtime and maximizing efficiency.
Vacuuming Time Breakdown for AC System Components
The duration of vacuuming varies significantly depending on the component’s size and the complexity of the system’s connections. A thorough understanding of these variations allows for optimized vacuuming procedures and accurate troubleshooting. The evaporator, condenser, and compressor, being integral parts of the system, require different vacuuming times.
Expected Vacuuming Time for Different Components
The following table provides an estimated vacuuming time for various AC system components. These times are approximations and can vary based on specific vehicle models and system configurations. Properly accounting for the size and complexity of the component is crucial for accurate time estimation.
Component | Expected Vacuum Time (minutes) | Explanation |
---|---|---|
Condenser | 15-30 | The condenser, often large and with multiple connections, requires a longer vacuuming time to ensure complete removal of air and moisture. The time depends on the size and complexity of the condenser unit, as well as the number of fittings and connections. |
Evaporator | 10-20 | The evaporator, typically smaller than the condenser, generally requires less vacuuming time. However, the complexity of the connections and the presence of internal components can influence the total time. |
Compressor | 5-10 | The compressor, being a sealed unit, requires the shortest vacuuming time. The time is largely determined by the system’s connections and any associated leaks. Typically, the vacuum time is minimal once the connections are properly secured and the compressor is properly isolated. |
Expansion Valve | 5-10 | The expansion valve, a critical component for regulating refrigerant flow, requires a short vacuum time, often comparable to the compressor. |
Visual Aids and Diagrams
Visual aids, such as diagrams and flowcharts, are crucial for effectively understanding and troubleshooting automotive air conditioning (AC) vacuuming procedures. Clear illustrations of system components and refrigerant flow pathways aid in identifying potential issues and ensuring proper execution of the process. Accurate diagrams also highlight the importance of correct connections, which directly impact the effectiveness and duration of the vacuuming process.
Schematic Diagram of Car AC System
A schematic diagram illustrating the car AC system components involved in the vacuuming process provides a comprehensive overview. The diagram should clearly depict the compressor, condenser, evaporator, expansion valve, accumulator, and associated tubing. Labels should indicate the direction of refrigerant flow during the vacuuming process, emphasizing the sealed system and the role of each component.
Refrigerant Flow Diagram During Vacuuming
A schematic diagram depicting the flow of refrigerant during the vacuuming process is essential. This diagram should visually represent the refrigerant’s movement through the system components. Arrows should indicate the direction of the vacuum pump’s suction, highlighting the areas being evacuated. The diagram should explicitly show the sealed system configuration, highlighting the crucial role of proper connections in maintaining a vacuum.
For example, a leak in the system’s tubing or fittings will directly impact the effectiveness of the vacuuming process.
Importance of Correct Connections
Correct connections between components are paramount to achieving an effective vacuum. Improper connections can create leaks, hindering the vacuuming process. This is critical because any leak will allow air to enter the system, reducing the achievable vacuum level and potentially leading to inaccurate readings. In addition, improper connections, such as loose fittings or damaged hoses, can result in the need for repeated vacuuming attempts.
Flowchart for Vacuuming Procedure
A flowchart detailing the steps in the vacuuming procedure can guide technicians through the process effectively. This visual representation helps ensure a standardized approach and reduces the risk of errors.
Step | Description |
---|---|
1 | Inspect and prepare the AC system. Ensure all components are accessible and any loose connections are tightened. |
2 | Connect the vacuum pump to the appropriate port on the AC system. |
3 | Turn on the vacuum pump and monitor the vacuum gauge reading. Ensure the vacuum reading reaches the target pressure. |
4 | Disconnect the vacuum pump and seal all ports. |
5 | Verify the vacuum level is maintained over a specific time frame, usually 30-60 minutes, as per the recommended duration for the system. |
6 | Record the final vacuum reading and document the entire process. |
Final Wrap-Up
In conclusion, determining the appropriate vacuuming time for a car’s AC system hinges on several interacting variables. The provided information offers a structured approach to the process, considering factors like vehicle characteristics, refrigerant type, system condition, and pump specifications. By adhering to the Artikeld procedures and troubleshooting guidelines, technicians and users can optimize the vacuuming process, ensuring efficient and long-lasting AC system operation.
FAQ Explained
What is the typical vacuuming time range for a standard sedan?
The typical vacuuming time for a standard sedan is between 30-60 minutes, but this can vary depending on the factors listed in the detailed analysis.
How does the type of refrigerant affect vacuuming time?
Different refrigerants have varying vapor pressures, influencing the rate at which the system evacuates. Specific data regarding the effect of different refrigerants on the vacuuming process is presented in the detailed analysis.
What are common mistakes to avoid during the vacuuming process?
Common mistakes include inadequate leak detection, incorrect gauge readings, and improper use of the vacuum pump. The analysis provides a detailed list of these potential errors and how to avoid them.
What tools are needed for the procedure?
The required tools for the vacuuming procedure are Artikeld in the section detailing the procedure. These include a vacuum pump, gauges, and appropriate safety equipment.