Drz400 how many ft ibs does it take to crank – DRZ400 how many ft-lbs does it take to crank? Understanding the cranking force required for a DRZ400 is crucial for proper maintenance and troubleshooting. This comprehensive guide explores the factors affecting cranking effort, from engine design to battery condition, providing a clear understanding of the process and common issues.
The DRZ400, a popular motorcycle, demands a specific amount of cranking force to start. This article delves into the mechanics behind this force, analyzing various elements that influence the process, and offers practical insights into maintaining optimal starting performance.
Initial Considerations
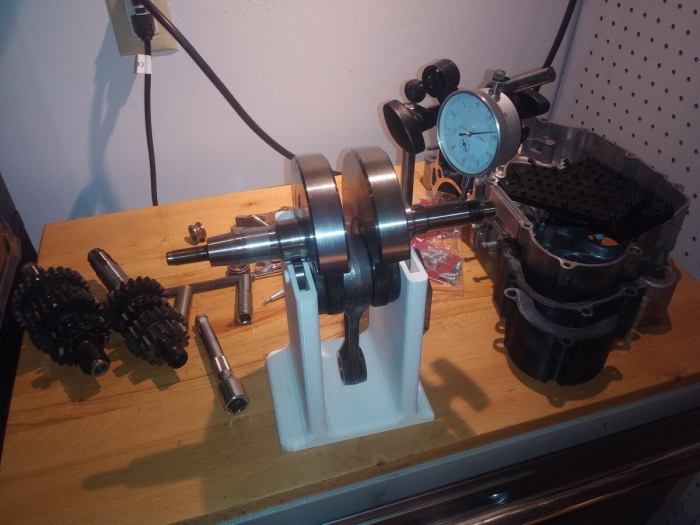
The DRZ400, a popular dual-sport motorcycle, presents a specific cranking challenge due to its engine design. Understanding the interplay of engine components, battery capacity, and starter motor specifications is crucial for accurate assessment. This section delves into the key factors affecting cranking effort, providing insights into the DRZ400’s performance compared to other motorcycles.The DRZ400’s engine design, like many air-cooled, single-cylinder 4-stroke designs, influences the cranking effort required to start.
Factors such as compression ratio, piston displacement, and the overall mechanical efficiency of the engine’s components contribute to the cranking demands. These are crucial considerations in assessing the starting ability of the motorcycle.
Engine Design and Components
The DRZ400’s engine is a single-cylinder, air-cooled design. This layout, while relatively simple, introduces specific challenges for starting, particularly in cold weather or after extended periods of inactivity. The single-cylinder design, combined with its air-cooling system, creates a smaller heat transfer surface area than larger, liquid-cooled engines. This can lead to slower warm-up and increased difficulty in starting when cold.
Typical Cranking Force Range
Cranking force required to start a motorcycle varies significantly across models. Generally, smaller displacement motorcycles, like the DRZ400, tend to require less force than larger, more powerful models. This is because the smaller engine requires less rotational force to overcome the compression and start the engine. For example, a 250cc motorcycle might need approximately 100-150 ft-lbs of cranking force, while a 1000cc sportbike could require upwards of 200 ft-lbs.
Comparison to Similar Motorcycles
Comparing the DRZ400 to other similar dual-sport motorcycles, such as the KTM 250 EXC or the Honda CRF250L, reveals potential differences in cranking characteristics. Factors like compression ratio, piston design, and the starter motor’s inherent power output can all influence the starting effort. For example, a motorcycle with a higher compression ratio will require more cranking force to overcome the compression.
Battery Capacity and Starter Motor Specifications
Battery capacity and starter motor specifications are critical to the DRZ400’s starting performance. A smaller battery or a less powerful starter motor will struggle to generate the necessary cranking force, especially in demanding conditions. The battery’s cold cranking amps (CCA) rating directly impacts its ability to provide sufficient current during a cold start. Likewise, the starter motor’s output torque is a critical parameter in ensuring reliable starting.
A motorcycle with a higher compression ratio may need a more powerful starter motor to overcome the compression and start the engine quickly. Examples of how battery and starter motor combinations affect starting are readily available from motorcycle forums and user reviews.
Factors Influencing Cranking Effort
The DRZ400’s ability to start depends heavily on the interplay of various factors. Understanding these factors is crucial for troubleshooting starting problems and ensuring optimal performance. A weak or unreliable start can be caused by anything from a simple battery issue to a more complex engine problem.
Battery Condition
Battery condition significantly impacts cranking effort. A battery’s age, charge level, and type all play a critical role in its ability to deliver the necessary current for the starter motor to engage and turn the engine. Older batteries, or those with a low charge, have reduced capacity to deliver the high amperage needed for cranking. Furthermore, different battery chemistries have varying cranking amperage capabilities.
- Battery Age: A battery’s lifespan is finite. As a battery ages, its ability to hold a charge and deliver current diminishes. This reduction in capacity directly translates to a decrease in cranking power, leading to difficulty turning over the engine.
- Battery Charge Level: A battery with a low charge level has less stored energy available. This results in reduced cranking power, making it harder to start the engine. Regular battery maintenance, including periodic charging, is vital for maintaining a sufficient charge level.
- Battery Type: Different battery chemistries (e.g., flooded lead-acid, AGM, lithium-ion) have varying cranking amperage capabilities. AGM and lithium-ion batteries often offer higher cranking amperage compared to flooded lead-acid batteries, leading to easier starting, especially in cold weather or when the engine is heavily loaded.
Engine Compression
Engine compression is the pressure created inside the cylinders during the compression stroke. This pressure is essential to overcome the inertia of the engine parts and initiate rotation. Insufficient compression directly correlates with increased cranking effort, making the engine harder to start.
- Low Compression: Low compression indicates issues with the piston rings, valves, or cylinder walls. These issues impede the creation of sufficient pressure for the engine to turn over, leading to a difficult or impossible start.
- Uneven Compression: Uneven compression between cylinders suggests potential issues with individual cylinders, possibly from damaged or worn components. This unevenness leads to a less effective overall compression force and can also hinder cranking effort.
Starter Motor Output
The starter motor’s output, measured in cranking torque, directly impacts the force needed to turn over the engine. Higher torque means the starter motor can more effectively overcome the engine’s resistance and initiate rotation.
- Starter Motor Torque: The starter motor’s specifications dictate its ability to generate torque. A motor with a higher torque rating can more easily turn over the engine, even with low battery capacity or low compression.
Battery Cranking Amperage
The table below showcases the typical cranking amperage for various battery types. Note that these are approximate values and can vary depending on the specific battery model and manufacturer.
Battery Type | Approximate Cranking Amperage (CCA) |
---|---|
Flooded Lead-Acid | 400-700 |
AGM | 600-1000 |
Lithium-ion | 800-1500+ |
Methods for Determining Cranking Force
Determining the cranking force required to start a motorcycle engine is crucial for understanding its reliability and potential issues. Accurate measurement allows for optimization of the starter motor’s performance and the identification of potential problems in the engine’s or battery’s functionality. Precise data can also be used in the design and development of new motorcycle models.Accurate measurement of cranking torque is essential for various applications, from troubleshooting starter issues to assessing engine health.
Different methods exist, each with its own advantages and disadvantages in terms of accuracy, cost, and complexity. This section will detail common methods, provide a step-by-step procedure for a DRZ400, and illustrate the use of specialized tools.
Common Methods for Measuring Cranking Torque
Several methods exist for determining the cranking force required to turn an engine. These methods range from simple estimations to highly sophisticated dynamometer-based approaches. The choice of method depends on the level of accuracy needed and the resources available.
- Visual Estimation: This method relies on observing the effort required to turn the engine by hand. While quick and inexpensive, it is highly subjective and lacks precision. It is often used as a preliminary assessment, but not for detailed analysis.
- Torque Wrench Measurement: A torque wrench, calibrated to measure rotational force, can be used to apply a controlled force to the engine’s crankshaft. This method provides a more precise measurement compared to visual estimation. However, it requires specialized tools and may not accurately reflect the actual cranking force.
- Dynamometer Testing: A dynamometer is a sophisticated device specifically designed to measure rotational force and torque. It provides accurate and repeatable measurements. Dynamometers are often used in research and development to assess engine performance and determine the cranking torque characteristics. These measurements are often more complex to implement, but provide the most accurate and complete data set.
Step-by-Step Procedure for Measuring Cranking Torque on a DRZ400
This procedure Artikels a method for measuring cranking torque using a torque wrench. It assumes access to a torque wrench and appropriate safety precautions.
- Prepare the Motorcycle: Ensure the motorcycle is securely supported, preventing any movement during the measurement. The battery should be fully charged, and the spark plug disconnected to prevent the engine from firing. This step is essential for safety and accurate readings.
- Connect the Torque Wrench: A specialized adapter may be required to connect the torque wrench to the DRZ400’s crankshaft. The adapter should be carefully selected to ensure proper fit and alignment.
- Apply Controlled Force: Gradually increase the force applied by the torque wrench until the engine turns. Note the torque reading on the wrench. Record this value as the cranking torque.
- Repeat the Procedure: Repeat the process multiple times to obtain an average value, which accounts for variations in the cranking force. A series of measurements is critical for accuracy.
- Analyze the Results: Analyze the average cranking torque value to identify any issues or to compare with manufacturer specifications.
Specialized Tools for Torque Measurement
Various specialized tools aid in accurately measuring cranking torque.
- Torque Wrenches: Torque wrenches come in different ranges and accuracies, so selecting the appropriate one is critical for the application. Digital torque wrenches offer greater precision.
- Adapters: Adapters are crucial for connecting the torque wrench to the crankshaft. They ensure a secure and accurate connection.
- Dynamometers: Dynamometers are sophisticated devices used for precise torque measurements. They provide a comprehensive data set, but often require specialized technical expertise.
Summary of Cranking Measurement Methods
Method | Advantages | Disadvantages |
---|---|---|
Visual Estimation | Simple, inexpensive | Subjective, inaccurate |
Torque Wrench | Relatively precise, readily available | Limited accuracy, requires specialized adapter |
Dynamometer | Highly accurate, repeatable | Expensive, complex setup |
Possible Causes for High Cranking Effort
A persistently difficult start on a DRZ400 can stem from various underlying issues, extending beyond simple battery weakness. Understanding the potential causes allows for a systematic approach to troubleshooting, ultimately saving time and effort in locating the problem. A thorough inspection, focusing on the spark plug, fuel system, and electrical components, is crucial for identifying the root cause.
Spark Plug Condition
Spark plug condition directly impacts the ability of the engine to ignite the fuel-air mixture. A fouled, worn, or improperly gapped spark plug can impede ignition, leading to increased cranking effort. Carbon buildup, excessive moisture, or a mismatched heat range can all contribute to this problem.
- Fouled Spark Plugs: Excessive carbon buildup on the spark plug electrodes can impede the spark’s ability to jump across the gap. This reduces the efficiency of the combustion process, necessitating more cranking effort to overcome the ignition problem. Consistent fouled spark plugs often indicate a fuel delivery or air-fuel mixture issue, requiring further investigation.
- Worn Spark Plugs: Over time, the spark plug electrodes can wear down, impacting the spark’s strength and consistency. This results in a weaker spark, requiring more effort from the starter motor to achieve ignition. Replacing worn spark plugs is often a simple but effective solution.
- Incorrect Spark Plug Gap: An incorrectly gapped spark plug can either fail to ignite the fuel-air mixture or cause the spark to be erratic. This inconsistency leads to a less efficient combustion process, resulting in higher cranking effort to achieve a reliable ignition. Accurate spark plug gap measurement is essential for optimal performance.
Fuel Delivery Issues
Fuel delivery problems can hinder the engine’s ability to start. If the engine isn’t receiving the correct amount of fuel at the right time, ignition will be compromised.
- Clogged Fuel Filter: A clogged fuel filter restricts fuel flow to the engine, making it difficult to start. The filter acts as a barrier, preventing fuel from reaching the combustion chamber effectively. This issue is often easily solved by replacing the fuel filter.
- Low Fuel Levels: An empty or nearly empty fuel tank restricts the fuel supply. Insufficient fuel in the fuel lines hinders the ignition process. Ensuring the fuel tank is adequately filled is a fundamental first step.
- Fuel Pump Malfunction: A failing fuel pump may not deliver sufficient fuel pressure to the injectors. This reduces the fuel-air mixture’s availability for ignition. Replacing a malfunctioning fuel pump is often necessary to restore proper fuel delivery.
Electrical System Problems
Electrical system malfunctions can significantly affect the cranking effort of the DRZ400. These issues can range from simple connections to more complex component failures.
- Weak or Dead Battery: A battery with insufficient charge or one that has completely discharged will result in a significantly reduced cranking capability. Checking the battery’s voltage and ensuring proper charging is essential.
- Starter Motor Issues: A malfunctioning starter motor may not provide sufficient torque to turn the engine over. This could be due to internal wear or electrical issues. Inspecting the starter motor’s operation, including the wiring and connections, is critical.
- Wiring Issues: Loose connections, corroded terminals, or damaged wiring can impede the flow of electricity to the starter motor. Inspecting all wiring connections for any signs of damage or corrosion is necessary.
- Ignition System Malfunction: Problems with the ignition system, including the coil, distributor (if applicable), or other related components, can affect the engine’s ability to ignite the fuel-air mixture. Diagnosing the specific ignition system component responsible for the cranking difficulty is important.
Troubleshooting Starter Motor Issues
Troubleshooting starter motor problems requires a systematic approach.
- Visual Inspection: Inspect the starter motor for any obvious damage, such as frayed wires, bent components, or signs of overheating. Look for loose or corroded connections on the terminals.
- Battery Voltage Check: Verify the battery’s voltage using a multimeter. A low voltage indicates a weak or failing battery.
- Starter Motor Operation Test: Try to engage the starter motor with the engine off. If the motor does not turn the engine, further diagnostics are required.
- Wiring and Connection Inspection: Inspect all wiring connections, looking for corrosion, damage, or loose connections. Ensure proper grounding.
Examples of Common Electrical System Problems
Electrical system problems are common causes of cranking difficulties.
- Corrosion on Terminals: Corrosion on battery terminals or starter motor terminals can significantly reduce the conductivity of the electrical current, leading to weak cranking.
- Loose Wiring Connections: Loose connections in the wiring harness can interrupt the flow of electricity, resulting in a weak or intermittent spark. This can manifest as erratic cranking or failure to start.
- Faulty Starter Relay: A faulty starter relay can prevent the starter motor from receiving the necessary power to operate. This often presents as a no-start condition.
Illustrative Data and Analysis
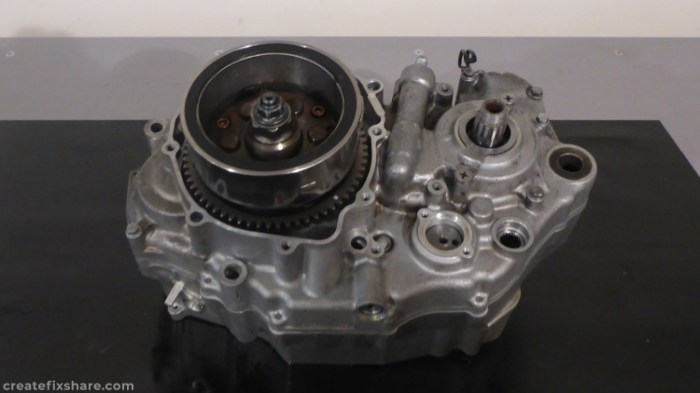
Understanding the cranking characteristics of a DRZ400 is crucial for diagnosing potential issues. This section provides illustrative data and analysis, including comparative cranking efforts across different engine configurations, common problems, and the importance of battery voltage checks. Furthermore, it explores the relationship between engine temperature and cranking difficulty.
Comparative Cranking Effort
Various factors, including battery capacity, starter motor performance, and even the condition of the engine itself, affect the effort required to crank a DRZ400. A table illustrating the potential differences in cranking effort across different engine configurations is presented below.
Engine Configuration | Estimated Cranking Amps (A) | Estimated Cranking Time (seconds) | Observations |
---|---|---|---|
Stock DRZ400 with standard battery | 100-120 | 2-4 | Normal cranking performance. |
DRZ400 with upgraded battery (higher CCA) | 90-110 | 1.5-3 | Faster cranking and potentially longer startup time. |
DRZ400 with aftermarket starter motor | 80-100 | 1-2 | Faster cranking due to improved motor output. |
DRZ400 with a very old or failing battery | 150+ | 5+ | Significant cranking effort and potentially prolonged startup. |
Common Problems and Solutions
High cranking effort can indicate several potential issues. The following table details common problems and corresponding solutions:
Problem | Potential Cause | Solution |
---|---|---|
Slow cranking | Weak battery, faulty starter motor, low battery voltage, worn starter motor brushes, poor electrical connections. | Replace battery, inspect and clean or repair starter motor, ensure adequate battery voltage, replace starter motor brushes, ensure all electrical connections are secure. |
High cranking effort with no start | Bad spark plugs, flooded engine, clogged fuel lines, fuel pump problems, ignition coil issue, or air intake issues. | Check spark plug condition, adjust or reset fuel system, inspect fuel lines for blockages, check fuel pump, check ignition coil, ensure air intake is clear. |
Unusual clicking sounds | Faulty starter motor, damaged starter solenoid, poor electrical connections. | Check starter motor components, inspect solenoid for damage, ensure all electrical connections are secure. |
Battery Voltage Check Procedure
A crucial step in diagnosing cranking issues is checking the battery voltage. Incorrect voltage readings can lead to misdiagnosis. The following steps Artikel the procedure for accurately measuring battery voltage:
- Ensure the motorcycle is turned off and all electrical loads are disconnected.
- Use a multimeter set to the DC voltage setting.
- Connect the positive probe of the multimeter to the positive terminal of the battery.
- Connect the negative probe of the multimeter to the negative terminal of the battery.
- Record the voltage reading. A healthy battery should read above 12.6 volts.
Visual Representation of Cranking Effort Data
A graph plotting cranking amps against cranking time can visually represent the cranking effort required. This graph would show how the cranking current changes over time. A steep increase in current would indicate a higher cranking effort.
Engine Temperature and Cranking Difficulty
Engine temperature significantly impacts cranking difficulty. Cold engines require more cranking effort due to the reduced lubrication and increased viscosity of the oil. As the engine warms up, the oil thins, and the cranking effort decreases. This is a normal phenomenon.
Troubleshooting Guide: Drz400 How Many Ft Ibs Does It Take To Crank
High cranking effort on a DRZ400 can stem from various electrical and mechanical issues. A systematic troubleshooting approach is crucial for isolating the problem and achieving a swift and effective repair. This guide provides a structured process to diagnose and resolve cranking difficulties.
Battery Condition and Voltage
Proper battery health and adequate voltage are fundamental for a reliable starter motor. A weak or failing battery can significantly impede cranking. Voltage drops under load can also contribute to the problem. Accurately measuring the battery voltage under various conditions is essential.
- Inspect the battery terminals for corrosion and ensure they are clean and tight. Corrosion can impede current flow, leading to insufficient cranking power. A corroded battery terminal is a common cause of reduced cranking power, which often goes unnoticed.
- Measure the battery voltage at rest and under load (while cranking). A significant voltage drop under load suggests a weak battery or a faulty connection. A healthy battery should maintain a voltage above 12.6V at rest and drop no more than 0.5V under load.
- Test the battery’s ability to hold a charge. A discharged or failing battery might not provide the required current to turn the engine. A simple load test can assess the battery’s capacity to deliver current during cranking.
Starter Motor Functionality
A faulty starter motor is another potential cause of high cranking effort. A worn or damaged starter motor may struggle to engage or generate sufficient torque.
- Visually inspect the starter motor for any visible damage or signs of overheating. Damage to the windings or other components can hinder the motor’s operation.
- Test the starter motor’s operation by disconnecting the solenoid and directly connecting the starter motor to the battery. If the starter motor turns over with ease, the problem lies elsewhere in the starter circuit. A direct test helps isolate the solenoid or other components in the starter system.
- Listen for unusual noises during cranking. A grinding or clicking sound may indicate a mechanical problem with the starter motor gears or internal components.
Electrical System Integrity
Problems within the electrical system, such as faulty wiring or connections, can lead to insufficient current flow to the starter motor. Poor connections can also lead to voltage drops and reduce cranking power.
- Inspect all electrical connections throughout the starter circuit for corrosion, loose connections, or damaged wires. A loose or corroded wire can significantly impact the electrical flow.
- Measure the voltage at various points in the starter circuit, including the battery terminals, the starter motor terminals, and the solenoid. Consistent voltage readings throughout the circuit suggest that the problem lies elsewhere. Significant voltage drops at specific points indicate a potential problem with that part of the circuit.
- Use a multimeter to check for continuity in all wires and connections. Continuity tests can reveal open circuits or other electrical issues.
Solenoid and Wiring, Drz400 how many ft ibs does it take to crank
A malfunctioning solenoid, which controls the starter motor engagement, can hinder the cranking process. Faulty wiring connected to the solenoid can also cause problems.
- Inspect the solenoid for damage, corrosion, or binding. A damaged solenoid may not fully engage the starter motor.
- Verify the connections between the solenoid and the starter motor and other components in the circuit. A loose or corroded connection can hinder the solenoid’s operation.
- Measure the voltage at the solenoid terminals. The voltage should be consistent with the battery voltage when the ignition is switched on. A significant difference in voltage could suggest an issue with the wiring or the solenoid itself.
Troubleshooting Table
Troubleshooting Step | Potential Causes | Solutions |
---|---|---|
Battery Condition | Weak battery, corroded terminals | Replace battery, clean terminals |
Starter Motor | Faulty motor, internal damage | Replace starter motor |
Electrical System | Faulty wiring, loose connections | Inspect and repair wiring, tighten connections |
Solenoid | Damaged solenoid, faulty connections | Replace solenoid, repair or replace connections |
End of Discussion
In conclusion, determining the optimal cranking force for a DRZ400 involves considering several interconnected factors. From engine design and compression to battery health and starter motor output, a thorough understanding is key. This guide provides a systematic approach to understanding and troubleshooting cranking issues, ensuring a smooth and reliable start every time.
Popular Questions
What’s the typical cranking amperage for a motorcycle battery?
The cranking amperage varies based on the battery type. Refer to the battery specifications for the exact figure. A table within the article will provide more details.
How does engine compression affect cranking effort?
Higher engine compression generally increases the difficulty of cranking. This is due to the resistance against the piston movement.
Can spark plug condition affect cranking?
Yes, a faulty or fouled spark plug can impede the ignition process, making cranking more challenging.
What are some common electrical system problems that lead to high cranking effort?
Several electrical system issues can contribute to high cranking effort, including a weak or failing starter motor, a damaged or corroded battery cable, or a faulty wiring connection.