How to wire a one wire alternator – How to wire a one-wire alternator? This guide provides a thorough and engaging exploration of this critical automotive electrical task. One-wire alternators, a departure from traditional multi-wire designs, offer unique advantages in terms of simplicity and cost-effectiveness. We’ll delve into the specifics of wiring, addressing common challenges and ensuring a safe and successful installation.
Understanding the intricacies of one-wire alternator systems is key to a flawless installation. From the fundamental differences in wiring to the specific tools and procedures, this comprehensive guide leaves no stone unturned. We’ll explore the underlying principles, practical applications, and troubleshooting tips, equipping you with the knowledge needed for a successful project.
Introduction to One-Wire Alternators
One-wire alternator systems represent a streamlined approach to vehicle electrical systems, offering a compelling alternative to traditional multi-wire setups. This simplification, while potentially reducing complexity, requires a thorough understanding of its operation and potential drawbacks. This discussion will explore the intricacies of one-wire systems, highlighting their advantages and disadvantages, and comparing them to their multi-wire counterparts.One-wire alternator systems, in contrast to the more conventional multi-wire systems, use a single wire to carry both the charging current and the signal for the voltage regulator.
This single wire approach drastically simplifies the wiring harness, reducing the potential for wiring errors and potentially saving on manufacturing costs. However, this simplification does not come without potential trade-offs. Understanding the specific needs of your application is crucial before adopting a one-wire system.
Fundamental Differences
The core difference lies in the wiring configuration. Multi-wire alternators employ separate wires for charging current and voltage regulation signals. This separation allows for more independent control and monitoring, but also results in a more complex wiring network. One-wire systems, on the other hand, combine these functions into a single wire, significantly reducing the overall wiring complexity. This simplification is achieved through specific voltage regulator designs that interpret the charging current signal to maintain proper charging output.
Advantages of One-Wire Alternators
One-wire systems often offer several advantages:
- Reduced Wiring Complexity: The single wire approach simplifies the wiring harness, making installation and maintenance potentially faster and easier. Fewer connections mean less potential for wiring errors, and this is particularly beneficial in applications with limited space or challenging access to the alternator.
- Potential Cost Savings: Fewer wires and components translate to reduced manufacturing costs and, in some cases, potentially lower installation costs for the vehicle owner. This simplification can also translate to reduced materials usage.
- Improved Reliability (Potentially): With fewer connections, the potential for electrical issues due to poor connections or corrosion is reduced, leading to improved system reliability. However, this benefit can be mitigated by the need for specialized regulators and wiring.
Disadvantages of One-Wire Alternators
Despite the advantages, one-wire systems also present potential drawbacks:
- Increased Sensitivity to Wiring Errors: While fewer wires reduce potential issues, a single wire fault can potentially disrupt the entire charging system. Proper installation and careful attention to wiring are crucial for optimal performance.
- Requirement for Specialized Components: The unique charging system demands specialized voltage regulators that can interpret the charging current signal. This often leads to higher component costs compared to traditional multi-wire systems.
- Potential for Charging System Malfunctions: A fault in the voltage regulator, which is specific to one-wire systems, can result in the charging system malfunctioning. This can lead to reduced alternator output or even system failure if not addressed quickly.
Examples of Vehicles Using One-Wire Alternators
One-wire alternators are found in a variety of vehicles, including some light trucks, SUVs, and even certain marine applications. The specific prevalence and usage depend on the design choices of the vehicle manufacturer. A wide range of manufacturers and vehicle types have utilized one-wire systems in various models, demonstrating the viability of this technology in diverse applications.
Comparison of One-Wire and Multi-Wire Alternators
Feature | One-Wire Alternator | Multi-Wire Alternator |
---|---|---|
Wiring Complexity | Lower | Higher |
Cost | Potentially higher (due to specialized components) | Potentially lower |
Maintenance | Potentially easier (fewer connections) | Potentially more complex (more connections) |
Understanding the Wiring Diagram
Unraveling the mysteries of a one-wire alternator system begins with a thorough understanding of its wiring diagram. This diagram, a roadmap to the electrical heart of your vehicle, visually depicts the flow of current and the intricate relationships between components. Mastering this diagram is crucial for accurate installation and troubleshooting, ensuring optimal performance and longevity of your charging system.The one-wire alternator wiring diagram differs significantly from traditional multi-wire systems.
It simplifies the charging circuit by utilizing a single wire to manage both the charging and grounding functions. This simplification often leads to a more compact and efficient system, but it requires a deeper understanding of the unique roles of each component.
Key Components of a One-Wire Alternator Wiring Diagram, How to wire a one wire alternator
The diagram meticulously Artikels the components involved in the charging circuit. These components, like the alternator itself, the battery, and the voltage regulator, are interconnected by wires, ensuring the smooth flow of current. Understanding their roles is essential to interpreting the diagram correctly.
Function of Each Component in the Circuit
The alternator, the heart of the charging system, converts mechanical energy into electrical energy, generating the power needed to recharge the battery. The voltage regulator acts as a critical control unit, maintaining a stable output voltage, preventing overcharging and protecting the electrical system from damage. The battery stores the generated electricity, supplying power to the vehicle’s electrical components.
Importance of Accurate Wire Identification
Precise identification of wires and terminals is paramount for successful installation and troubleshooting. Incorrect connections can lead to system malfunction, damage to components, and potentially dangerous situations. Each wire plays a specific role in the circuit, and improper connections can lead to a chain reaction of issues.
Typical Wire Colors and Functions
The table below provides a common reference for wire colors and their corresponding functions within a one-wire alternator system. These colors help in the identification and connection of specific wires to the correct terminals, crucial for a functional charging system.
Wire Color | Function |
---|---|
Red | Positive terminal (usually connected to the alternator’s output terminal) |
Black | Grounding wire |
Yellow | Alternator output terminal (or other alternator specific) |
Green/Yellow | Voltage Regulator terminal (often specific to the vehicle’s design) |
Types of Connectors and Their Purposes
Different types of connectors serve specific purposes in the one-wire alternator system. Understanding these connectors and their function is critical for a successful connection and troubleshooting.
Connector Type | Purpose |
---|---|
Ring Terminals | Securely connecting wires to alternator terminals, often in the alternator’s output wire |
Crimp Connectors | Providing a secure connection between wires, ensuring proper electrical contact |
Butt Connectors | Joining two wires together to extend the wire length |
Splice Connectors | Joining two wires together, often for repair or modification |
Tools and Materials Needed
Crafting a robust and reliable one-wire alternator system demands meticulous preparation. Proper selection of tools and materials is paramount to ensuring a safe and efficient installation. The correct tools prevent damage to components, minimize risks, and ultimately lead to a better finished product. High-quality materials are essential for lasting performance and dependability.
Essential Tools
Careful selection of tools is crucial for the success of the project. Improper tools can lead to damage, wasted time, and safety hazards. The right tools streamline the process and ensure precision in every step.
- Screwdrivers (Phillips and flathead): Essential for disassembling and reassembling components. Different sizes are needed for various screws and fasteners. Ensure that the screwdrivers are in good condition to prevent slippage and potential damage.
- Wire strippers: These are vital for precisely removing insulation from wires without damaging the conductor. Accurate stripping prevents short circuits and ensures proper connections.
- Crimping tool: Used to secure wire connectors, this tool is indispensable for a strong and reliable connection. Using a crimping tool ensures that the connectors are securely fastened, preventing loose connections that can cause malfunctions.
- Multimeter: A multimeter is critical for verifying voltage and current levels during the installation. This ensures proper operation and prevents potential issues.
- Pliers (needle-nose and slip-joint): Useful for handling small parts, bending wires, and gripping components. Different types of pliers are necessary for handling various components during the installation process. Using the correct pliers for each task minimizes the risk of damage to the wires and connections.
- Wire cutters: Essential for cutting wires accurately and cleanly. Sharp wire cutters prevent frayed wires and ensure proper connections.
Safety Equipment
Prioritizing safety is paramount in any electrical project. Using appropriate safety equipment mitigates risks and protects against potential hazards.
- Safety glasses: Protect your eyes from flying debris and potential electrical sparks.
- Gloves: Protect your hands from cuts and electrical shocks.
- Work bench: A sturdy work surface is important for stability and preventing accidents during the installation process. A sturdy workbench provides a stable platform for working on the project, minimizing the risk of components falling or being damaged.
Necessary Materials
The selection of high-quality materials directly impacts the reliability and longevity of the alternator system.
- Appropriate wire gauge: Select the correct wire gauge based on the alternator’s specifications. Choosing the correct wire gauge ensures that the system can handle the required current without overheating.
- Wire connectors: Choose high-quality connectors that are compatible with the wire gauge. High-quality connectors are essential to prevent corrosion and ensure reliable connections. Examples include ring terminals, spade connectors, and butt connectors.
- Insulation tape: Use high-quality insulation tape to wrap exposed wires and prevent short circuits. Proper insulation is crucial to preventing shorts and other electrical problems.
- Electrical tape: For securing wires and other electrical components. Use electrical tape for securing wires and other electrical components, to prevent shorts and other electrical problems. Choose electrical tape that is appropriate for the specific application.
Wiring Procedures
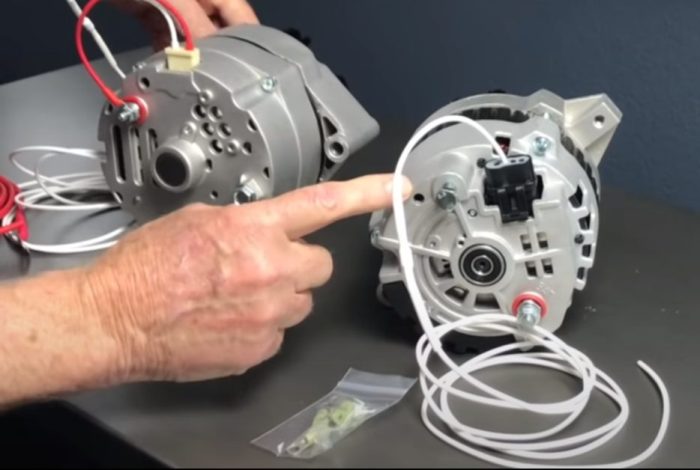
Embarking on the exciting journey of installing a one-wire alternator? Mastering the wiring procedure is crucial for a smooth and reliable operation. This section will guide you through the precise steps, ensuring a safe and efficient connection to your vehicle’s electrical system. Follow these steps diligently for a job well done.The intricate dance of connecting wires, ensuring proper grounding, and maintaining impeccable insulation are paramount for a properly functioning one-wire alternator.
Precise wiring ensures the alternator delivers optimal power to your vehicle’s electrical components.
Step-by-Step Connection Sequence
This detailed sequence Artikels the meticulous steps involved in connecting the one-wire alternator. Each step is vital to the overall success of the installation.
- Disconnect the Battery Terminals: Safety is paramount. Always disconnect the battery terminals before commencing any electrical work. This crucial precaution prevents accidental electrical shocks and safeguards your vehicle and personal safety. A properly disconnected battery will ensure a clean and safe work environment.
- Prepare the Mounting Location: Position the alternator on the designated mounting location and ensure secure attachment. Ensure proper alignment and stability. A securely mounted alternator will ensure long-lasting performance and reduce vibrations that could compromise connections.
- Connect the Ground Wire: Establish a solid ground connection by attaching the ground wire from the alternator to a clean, unpainted metal surface on the vehicle’s engine block. Proper grounding is essential for preventing electrical interference and ensuring a reliable electrical path. A secure ground connection ensures proper electrical flow.
- Connect the Alternator Wire: Carefully connect the wire from the alternator’s output terminal to the vehicle’s electrical system. This wire should be a heavy-duty gauge, capable of handling the alternator’s output. Connecting the alternator wire directly to the proper connection point ensures efficient power transfer.
- Secure Connections and Insulate: Use appropriate connectors and secure all connections with suitable clamps. Critically, ensure all connections are insulated properly to prevent short circuits. Proper insulation will safeguard your vehicle’s electrical system and prevent potential damage. Properly secured connections ensure reliability and longevity.
- Test the System: After completing all connections, reconnect the battery terminals. Start the vehicle and check the alternator’s output using a multimeter. This critical step confirms the alternator is functioning correctly and delivering the required power. A successful test indicates a proper connection and a working alternator.
Grounding Techniques
Grounding is a fundamental aspect of electrical systems. Proper grounding prevents electrical shorts and ensures the safe operation of electrical components.
- Direct Grounding: A direct ground connection involves attaching the wire to a solid metal part of the vehicle’s chassis or engine block. This approach provides a robust and reliable ground path.
- Grounding Points: Select a clean, unpainted metal surface for the grounding point. Avoid using areas with rust or corrosion. This ensures a consistent and reliable ground connection.
- Ground Wire Gauge: The ground wire’s gauge should match the alternator’s output to handle the current. A correctly sized wire ensures efficient power transfer.
Wiring Diagram Table
The following table illustrates the step-by-step sequence of connecting components for a one-wire alternator.
Step | Description | Image |
---|---|---|
1 | Disconnect the battery terminals. | (Imagine a diagram showing battery terminals being disconnected) |
2 | Prepare the mounting location for the alternator. | (Imagine a diagram of the alternator positioned on the vehicle) |
3 | Connect the ground wire from the alternator to a clean, unpainted metal surface on the engine block. | (Imagine a diagram illustrating the ground wire connection) |
4 | Connect the alternator wire to the vehicle’s electrical system. | (Imagine a diagram showing the connection of the alternator wire to the system) |
5 | Secure all connections and insulate thoroughly. | (Imagine a diagram highlighting secured connections and insulation) |
6 | Reconnect the battery terminals and test the system. | (Imagine a diagram showing the reconnection of the battery terminals) |
Troubleshooting and Common Problems
Embarking on a one-wire alternator wiring project can be incredibly rewarding, but like any intricate task, it may present a few challenges. This section delves into common issues you might encounter and provides practical solutions to get your system humming smoothly. We’ll arm you with the knowledge to diagnose and rectify problems, ensuring a reliable and efficient charging system.
Identifying Potential Issues
Troubleshooting a one-wire alternator system often involves a systematic approach. Carefully examining the connections and ensuring proper component function are key. Insufficient charging, system overloads, and voltage fluctuations are typical concerns. By understanding the potential pitfalls, you’ll be better equipped to address them effectively.
Diagnosing Problems
Diagnosing problems in a one-wire alternator system often starts with a methodical inspection of the wiring. Check for loose connections, frayed wires, and any signs of damage. A multimeter is an indispensable tool, allowing you to measure voltage and amperage to pinpoint issues accurately. A faulty diode, a poorly grounded connection, or an issue with the regulator can manifest as various problems.
Understanding the relationships between these components is crucial to pinpoint the source of the problem. Using the appropriate tools and following the wiring diagram meticulously is essential to achieve accurate diagnoses.
Solving Common Issues
This section Artikels common problems and provides solutions.
- Insufficient Charging: Insufficient charging often stems from a faulty alternator, a damaged wire, or a problem with the voltage regulator. Check the voltage output of the alternator at various engine speeds. If the voltage is consistently below the expected range, further inspection is warranted. A multimeter is essential to measure the voltage and ensure the alternator is functioning correctly.
Replace the faulty component, if necessary. Testing the system after each step is critical to ensuring effective charging.
- System Overloads: A system overload may be caused by a high draw from accessories or an incorrectly sized wire gauge. Identify the specific components drawing high current. Overloading can lead to overheating and damage to components. Ensure the wire gauge is appropriate for the current draw of the system. Adjusting the current draw by turning off unnecessary accessories can often resolve the issue.
- Voltage Fluctuations: Voltage fluctuations often arise from issues with the voltage regulator or the alternator itself. Inspect the regulator for damage and ensure its proper connections. Alternator problems, like a faulty diode or damaged bearings, can also contribute. Measure the voltage at different engine speeds and under varying loads to identify trends. If the problem persists, consult a professional technician.
Troubleshooting Table
Potential Problem | Cause | Solution |
---|---|---|
Insufficient Charging | Faulty alternator, damaged wires, voltage regulator issues | Inspect alternator output, check wire integrity, replace faulty regulator |
System Overload | High current draw from accessories, incorrect wire gauge | Identify high-draw accessories, upgrade wire gauge, reduce load |
Voltage Fluctuations | Faulty voltage regulator, alternator issues | Inspect regulator, check alternator for damage, consult a professional |
Importance of Testing
Thoroughly testing the system after each step is paramount to ensuring proper functionality. This allows for immediate identification of any introduced problems and enables precise adjustments. A comprehensive testing approach, using appropriate tools, will help guarantee the reliability and longevity of the one-wire alternator system.
Safety Precautions
Embarking on any electrical project demands unwavering respect for the potential hazards involved. Prioritizing safety throughout the one-wire alternator wiring process is paramount to ensuring a successful and incident-free outcome. By adhering to the safety precautions Artikeld below, you can minimize risks and enjoy the satisfaction of a job well done.Safe electrical practices aren’t just about avoiding accidents; they’re about preserving your well-being and ensuring the longevity of your project.
Understanding the importance of proper safety measures will make you a more confident and capable automotive technician.
Importance of Safety Precautions
Electrical systems, even seemingly simple ones, can harbor considerable dangers. A lapse in safety protocols can result in severe electrical shocks, burns, or even more serious consequences. Thorough preparation and adherence to safety guidelines are essential to mitigate these risks. These precautions safeguard your health and prevent potential damage to your vehicle’s electrical system.
Handling Electrical Components Safely
Always handle electrical components with care, avoiding contact with exposed wires or terminals. Ensure that your hands are dry and that you are wearing appropriate insulated gloves and safety glasses to protect against electric shock and flying debris. This proactive approach safeguards your health and minimizes the potential for harm.
Disconnecting the Battery
Disconnecting the battery is a critical safety step. This prevents unexpected electrical discharges and safeguards against accidental contact with energized parts. Before beginning any work on the vehicle’s electrical system, always disconnect the negative terminal of the battery first, followed by the positive terminal. This crucial step prevents accidental electrical shocks and ensures a safe working environment.
Using Appropriate Safety Equipment
Using the right safety equipment is non-negotiable. Wear insulated gloves and safety glasses to protect yourself from electrical shocks and flying particles. Ensure that your work area is well-lit and free of obstructions to prevent slips, trips, and falls. A well-equipped and organized workspace is an integral part of a safe working environment. Furthermore, ensure the proper use of safety glasses and insulated tools is practiced.
Emergency Procedures
Knowing what to do in case of an accident is just as crucial as preventing one. In the event of an electrical shock, immediately disconnect the power source. If someone is experiencing cardiac arrest, perform CPR. Know the location of the nearest emergency services and have a plan in place for contacting them in case of an emergency.
Emergency preparedness ensures a prompt and effective response to any unforeseen circumstances.
- CPR Training: Enroll in a CPR course to equip yourself with the knowledge and skills needed to respond to a medical emergency.
- First Aid Kit: Maintain a well-stocked first-aid kit in your vehicle or workspace to address minor injuries and provide immediate care.
- Emergency Contact List: Create a list of emergency contacts and keep it readily available for quick access in case of an emergency.
Additional Considerations: How To Wire A One Wire Alternator
Embarking on the rewarding journey of installing a one-wire alternator requires a keen eye for detail and a thoughtful approach. Beyond the fundamental wiring procedures, certain nuances and considerations can significantly impact the success and longevity of your project. This section dives into those important factors, providing you with the knowledge to tailor the installation to your specific vehicle and needs.
Vehicle-Specific Procedures
Different vehicles possess unique electrical systems and configurations. A thorough understanding of your vehicle’s electrical layout is paramount. For instance, older vehicles might require different grounding methods or adjustments for existing wiring harnesses. Modern vehicles, equipped with sophisticated electronics, often demand meticulous attention to signal compatibility and integrated systems. Consulting your vehicle’s repair manual is crucial for identifying any special procedures.
Adapting for Specific Applications
One-wire alternator systems, while generally adaptable, may necessitate adjustments for particular applications. For example, adding auxiliary accessories like power inverters or additional lighting systems will increase the electrical load on the alternator. Carefully assess the amperage requirements of your accessories to ensure the alternator can handle the increased demand. Overloading the alternator can result in reduced output and potentially damage the components.
Alternator Model and Configuration Considerations
Alternator models vary significantly in their internal components and specifications. Different models might have specific wiring arrangements, voltage regulator types, or even different mounting configurations. Consult the alternator’s manufacturer’s specifications for detailed information, including the appropriate voltage regulator for the application. This ensures proper charging and system stability. Incorrect choices could lead to inefficient charging, damage to the electrical system, and reduced battery life.
Customizing for Electrical Accessories
Integrating various electrical accessories into your one-wire alternator system demands careful planning. For instance, if you’re adding a winch, you’ll need to calculate the additional amperage draw. Similarly, incorporating LED lighting will often require adjusting the voltage regulator or incorporating a dedicated circuit. Properly sizing the wire gauge and using fuses to protect your accessories is essential to prevent overheating and potential system damage.
A well-designed electrical system anticipates and addresses potential load fluctuations. Consider the following:
- Amperage Requirements: Accurately determine the amperage demands of each accessory to ensure the alternator’s output capacity is sufficient.
- Wire Gauge Selection: Choose appropriate wire gauges to handle the amperage flow without excessive voltage drop, preventing potential overheating and damage.
- Fusing Strategies: Employ fuses to protect sensitive components from excessive current, safeguarding against potential short circuits and system failures.
- Dedicated Circuits: For high-demand accessories, consider dedicated circuits to isolate them from other components and prevent overloading.
Final Wrap-Up
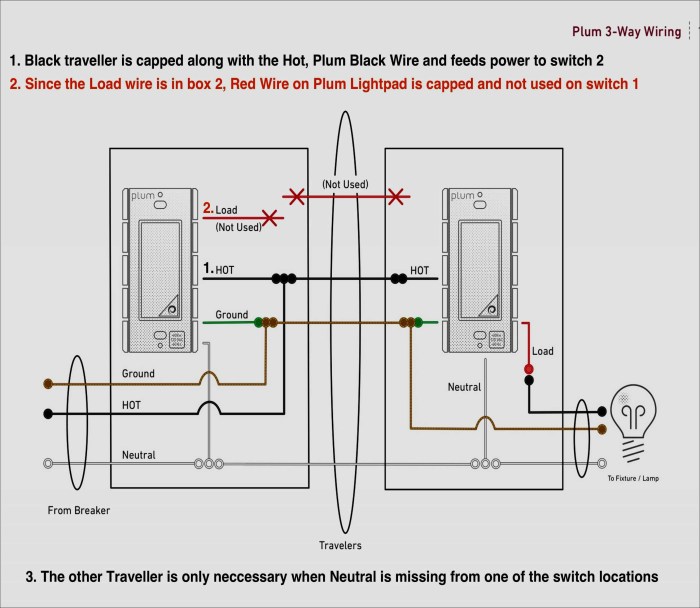
In conclusion, wiring a one-wire alternator involves a methodical approach that requires understanding the system’s components, tools, and safety procedures. This comprehensive guide provides a step-by-step approach, addressing both the theoretical and practical aspects. By following the provided instructions and safety guidelines, you can successfully wire your one-wire alternator, ensuring optimal performance and longevity for your vehicle’s electrical system.
FAQ Insights
Q: What are the typical wire colors used in a one-wire alternator system?
A: While wire colors can vary slightly by manufacturer, common colors for one-wire alternator systems often include red, black, and yellow. Refer to the specific wiring diagram for your alternator model for precise color codes.
Q: How do I know if the alternator is charging properly after installation?
A: A multimeter is essential for checking the alternator’s output voltage. With the engine running, measure the voltage at the battery terminals. Normal charging voltage should be within the specified range for your vehicle.
Q: What are some common causes of insufficient charging in a one-wire alternator system?
A: Faulty connections, damaged wires, or a malfunctioning regulator are common causes of insufficient charging. A thorough visual inspection and electrical tests can pinpoint the problem.
Q: What safety precautions should I take while working with electrical components?
A: Always disconnect the battery negative terminal before any electrical work. Wear appropriate safety gear, such as insulated gloves and eye protection. Work in a well-ventilated area and avoid working in wet conditions.